兰州石化公司原炼油厂(2021年6月份拆分炼油运行一部、二部、三部,以下称炼油运行部)为燃料—润滑油型炼油生产单位,一次原油加工能力为1050万吨/年,拥有常减压、重油催化、延迟焦化等39套生产装置,主要生产汽油、柴油、航煤、润滑油基础油、石蜡等10大类产品。炼油运行部前身是中国石油平衡西部原油资源、应对劣质复杂原油的加工基地和重要“调节阀”,在经历了多次扩建和技术改造的基础上,技术水平持续提升,形成了以清洁化生产和优化重油加工为主的千万吨级炼油厂。
近年来,伴随新能源行业的激烈竞逐,炼油行业已正式进入微利时代。在经济新常态下,如何做好炼油管理再升级、转变发展模式、调整优化结构、转换增长动力是当前需要解决的首要矛盾。积极响应公司全面预算管理相关规定,将全面预算管理与炼油生产经营有机结合、无缝链接、深入推进炼油全面预算管理,打造炼油生产经营管理2.0升级版有其必然性与必要性。
管理学上通常认为,全面预算管理是为数不多的几个将企业全方位、全过程、全员、全要素有机融为一体的重要管理手段。全面预算管理是指企业以发展战略为导向,根据对未来经营环境的预测,确定预算期内经营管理目标,并逐层分解、下达到企业内部各个经济单位,以价值形式反映企业生产经营和财务活动的计划安排。
炼油装置全要素成本主要包括产成品、辅助材料、燃料、动力、人工费用、制造费用等生产成本(见图1)和管理费用、“五项费用”等非生产性支出。炼油运行部共有12个区域39套装置均涉及生产成本,辅料成本主要集中在两套催化、重整等用催化剂装置及常减压、双脱等加注化工助剂装置;39套装置均涉及动力成本,主要集中在蒸汽、循环水和电力消耗较大的催化、重整、加氢装置,其中300万吨/年重催装置的烟机长周期运行对全厂蒸汽、电力的动力成本起决定性作用;39套装置、146个班组均涉及非生产性支出。在提质增效的大背景下,炼油运行部瞄准全要素成本,以市场为导向、以效益为中心,以超常规举措应对低油价冲击,全力打好提质增效实现保卫战。
一、实施背景与意义
作为公司炼化业务主要盈利单位,炼油装置开展全要素成本管控,不仅能提高经济效益,而且还可以发现装置在生产过程中存在的问题,以便于实现装置安全生产,从而推动企业整体效益最大化。
(一)炼油全要素成本管控是应对风险挑战的重要手段
在石化产品需求动力不足、低油价下拼的就是低成本、高质量,采取全要素成本管控势在必行。
(二)炼油全要素成本管控是实现效益最大化的有效途径
2021年,兰州石化公司提出开展提质增效专项行动,明确提出降低成本费用,炼油完全加工费控制在134.0元/吨以下,炼油吨油辅材≤15.39元/吨,确保利润最大化。作为公司主要生产单位,只有针对性地对可控成本进行控制,规避不必要成本费用的流出,在整体上才能符合企业长远战略发展目标,在细节上才能符合企业战略部署需求,通过建设出层次分明的成本管理框架,在不阻碍效益实现的基础上对成本费用进行优化控制,从根源上实现提质增效。
(三)炼油全要素成本管控是实现精益目标的现实需要
公司提出严格管理出效益,精细管理出大效益,精益管理出更大效益的理念。为了顺应越来越细、越来越精、越来越严的管理要求,只有在装置上才能突出操作的准确性,降低生产环节的浪费和消除不稳定因素,保证装置稳定运行;在专业上突出管理的细化和优化,确保管理的精益求精,才能实现整体效益最大化。作为公司主要生产单位,炼油运行部必须强化全要素成本管控,大幅削减成本,推进提质增效向纵深发展。
二、主要内涵
炼油全要素成本管控体系的构建,遵循了集团公司“精打细算、精耕细作、精雕细刻、精益求精”原则,聚焦兰州石化公司“严格管理出效益,精细管理出大效益,精益管理出更大效益”理念,其创新点主要表现为:
1. 成立利润中心,以事前算赢降成本。通过有机链接成本费用的事前预算、事中监控和事后总结,可以精算账、细算账、实算账,从而算出最佳资源组合。1个成本管控中心和38个装置成本构成利润中心小组,坚持“日监控、旬核实、月监督”及周例会制度,主动作为、靠前服务,通过“四查”分析会、经济运行分析会等,及时协调解决生产过程中出现的问题,使生产方案精准运行。
2. 盯住关键环节,以提高成果产出降成本。将提高产品管控质量、提高产品收率作为成本管控的重要环节,坚持产品高端化、精细化的思路,成功开发出PX级二甲苯、100LL高品质航空汽油、UL91无铅航空汽油和100vLL低铅航空汽油4项高效新产品。
3. 强化系统思维,以共享互通降成本。打破观念、突破局限,站在全局的角度考虑问题,努力向系统思维要效益。牺牲装置发电指标,主动承担起公司炼油区蒸汽系统的平衡任务,实现了动力厂锅炉房单炉运行的“一炉一线”目标。眼睛向内,将催化锅炉排污水、两套硫磺装置外排废水、各空冷排污水综合回收利用,作为催化装置烟气脱硫用水,优化装置互联降成本。按同类型设备运行的相关性,在设备的缺陷管理,预防性维护、预防性维修等各类运行工况中实现互通互联、数据共享,降低了设备采购成本。
4. 紧盯生产要素,压实全价值链降成本。炼油运行部以效益最大化为中心,把成本费用的事前预算、事中监控和事后总结有机链接,精算账、细算账、实算账,算出最佳资源组合,通过减柴增汽、控损增效,辅材管控、控辅增效,“控总抓小盯柴油”降低燃动压费创效,“人员增值、停工降本”控制固本、降本增效,打开费用、制造对账、对标增效全价值链举措,引导一切资源向效益流动,一切工作向效益聚焦,推动生产运行向精益转型,做到运行成本最优。
三、主要做法
以集团公司主题教育为契机,以全年挖潜增效为目标,坚持低成本发展策略,盯紧效益增长点和出血点,在全过程成本管控和产品结构优化方面苦下功夫,对生产经营中核算、分析、决策控制各项成本,通过思想强基、管理提质、优化增效等多种科学管理手段不断攻关,打好降本提质“组合拳”,打赢成本管控“攻坚战”。主要做法具体表现为:
(一)以利润为中心,强化顶层设计
炼油运行部建立以利润为中心的管理模式,优化利润决策,形成以成本和效益管控指导生产运行的机制,为实现效益最大化提供支撑。
1. 成立机构,挂图作战。面对复杂多变的市场形势和“保增长保效益”的压力,积极贯彻落实公司“一起算效益账”工作部署,建立与战略目标相匹配的管理框架,成立了以生产副总工程师、生产科长统筹的“炼油成本利润中心”,包括38个装置成本和1个成本管控中心。成本利润中心以利润测算为导向,研究各项成本的构成,加强对收入、成本和利润的管控,全面提升全员效益意识和算账意识,让每个岗位、每个环节都成为效益之源,实现了全员、全流程、全要素成本管控,形成了两测算、一核算“2+1”成本测算管理模式。
2. 强化教育,转变观念。全要素成本管控的核心是全员解放思想、转变观念。分阶段、有重点、常态化开展形势任务宣讲,用详实数据和生动事例,从不同角度把提质增效问题讲透,把措施讲活,把中心任务讲明,参加人员达4886人次。
3. 细分专业,分级管控。炼油运行部按照职责,科学划分责任成本体系,按照各专业组的工作职责和工作流程,对于各项指标按照“谁主管、谁负责”的原则进行科学测算、精心细化,确立本单位的目标成本体系。指标体系按照归口管理原则进行管理,将总目标细化分为细小的,不可再分的分项目标成本,然后再将分项成本目标分解到各归口单位,各归口单位再将指标分解到责任单位,并以责任书、承包书的形式落实责任主体,同时将权利赋予各责任单位,使其具有费用的管控义务和考核权利,通过上报费用形成,对比分析,纠偏及考核,实现费用管控目标。
(1)生产工艺管理专业负责协调解决各装置利润测算所需的数据,协调公司计划处和财务处,及时为各装置提供投入产出数据和主要原料、产品价格等数据;(2)设备管理专业负责协调解决各装置维护修理费用、固定资产折旧及摊销费、检测费、试验检验费和物料消耗等设备专业相关费用的统计测算和分析;(3)安全管理专业负责协调解决各装置劳动保护费、警卫消防费等安全专业产生的相关费用的统计、测算和分析;(4)环保管理专业负责协调解决各装置排污费、三废处理费、运输费、环保三剂消耗费用、技术服务费等环保专业产生的相关费用的统计测算和分析;(5)人事管理专业负责协调测算员工成本的相关工作及分析;(6)办公系统专业负责协调解决各装置及机关的低值易耗品、差旅费、绿化及环境卫生费的统计、测算和分析;(7)各装置根据月度生产经营计划、结合装置生产运行实际,对各装置三剂消耗、动力消耗进行预测,负责对各装置的固定成本、生产成本、投入和产出、效益等费用进行测算和分析。
(二)以要素为基准,做好增效文章
炼油运行部以效益最大化为中心,把成本费用的事前预算、事中监控和事后总结有机链接,精算账、细算账、实算账,算出最优资源组合,通过全价值链降本增效举措,引导一切资源向效益流动,一切工作向效益聚焦,推动生产运行向精益转型,做到运行成本最优。
1. 运行优化,产销协调
优化运行是管理创效的重要支点。炼油运行部坚持“日监控、旬核实、月监督”及周例会制度,利润中心小组主动作为、靠前服务,及时协调解决生产过程中出现的问题,将功夫下在现场,眼睛盯住市场,生产人员时刻对油品市场保持高度关注,将“按需定产、高效高产、资源优化、氢气降本”作为优化运行的着力点。
坚持产品高端化、精细化的思路,2020年首次生产出PX级二甲苯和100LL高品质航空汽油。2021年4月份,为抢抓市场机遇,拓宽高效产品市场占有率,炼油运行部根据无铅和低铅航空汽油调和组分的质量标准要求,通过一系列操作调整,生产出高质量的航空异辛烷、180号航空洗涤汽油、商品级甲苯等调合组分,成功开发出UL91无铅航空汽油和100vLL低铅航空汽油2项高效新产品。4月底燃料油市场需求回暖,120万吨/年重催装置克服提前开工的诸多困难顺利喷油开工,实现“按需定产,错峰排产”,抢占市场需求先机。同时,针对炼油丙烯、三苯、异辛烷等市场紧俏、高附加值产品,挂牌督战,制定一揽子工艺攻关措施,催化丙烯收率及三苯收率较预算分别提高0.15%、1.89%,实现高效高产。再者,投产炼厂气提氢装置,将重整低压氢气通过炼厂气提氢装置增压变为高压氢气,解决炼油低压氢气过剩,高压氢气不足的掣肘难题,实现氢气资源优化利用。从效益测算来看,重整增压氢成本较原高压氢有明显价格优势,实现财务预算内增效5009.82万元。
2. 减柴增汽,控损增效
柴油额外量为炼油板块逆向倒逼各地区公司实施炼化一体化转型的重要抓手。柴油额外量价差对炼油运行部减利影响较大,截至9月份,柴油额外量比例为37.89%(图2),柴油额外量合计减利6.42亿元。目前,降低柴汽比仍是降低额外量影响的首选途径。
炼油运行部将提高产品收率作为成本管控的重要环节之一,通过持续拓展西南保税航煤市场,成功控制了90万吨/年柴油加氢装置的加裂航煤收率在32%以上;两套常减压装置控制常一线航煤、300万吨/年柴油加氢装置控制石脑油、300万吨/年重催装置控制稳定汽油终馏点在指标范围内。通过以上措施,炼油柴汽比已经自年初的1.38%,连续两个月稳定破“1”,完成值为0.91%,减少额外量21.17万吨,减少额外量价差减利1.67亿元。
3. 辅材管控,控辅增效
炼油运行部吨油辅材“十三五”期间大幅降低33.03%,2020年吨油辅材完成值为14.58元/吨,比板块均值17.62元/吨低3.04元/吨,在26家炼油生产企业中名列第八,同比上升2名,在7家炼化一体化企业中名列三甲,系历史最好水平。尽管2021年90万吨/年催化柴油加氢改质装置及气提氢装置按计划开工,全年吨油辅材预估为16.11元/吨,但控辅形势依旧严峻。炼油运行部坚持“一切成本均可降”的理念,推进全员、全过程辅材管控,挖掘降辅潜力,压缩辅材成本,实现辅材费用刚性硬下降。
从2020年全年辅料费用占比来看,催一、催二及汽、柴油加氢车间合计占辅料费用的86.78%,控制以上车间辅料费用,即控制两套催化裂化催化剂单耗,以及固定床催化剂延期仍是炼油控辅优先方向。控制催化裂化催化剂单耗,通过工艺难题攻关,实现5套装置10种固定床催化剂延期使用、1种固定床催化剂国产化。在用33种消耗类三剂对标消耗定额,进行科学、按需加注;对二类三剂,按照制度进行“比价格、比技术、比质量、比业绩”“四比”拓展引入。通过降低两套重催装置催化裂化催化剂单耗、延长固定床催化剂使用周期、烟气脱硝催化剂国产化等多管齐下,严格控制2021年吨油辅材在15.39元/吨以内,创标目标15元/吨。
4. 降低燃动,压费创效
从分析炼油运行部2020年完全加工费130.59元/吨来看,其中吨油燃动成本占比为34.22%,降低燃动成本已成为降本压费的重要抓手。“降燃动”的战术目标明确:“控总、抓小、盯柴油”,即“控住总额,抓住小项、紧盯柴油”。将燃动成本总量性指标逐层分解、压力逐层传递,压茬推进实现抱起西瓜“控住总额”;实施专人“日跟踪、周小结、月盘点”动力消耗管理模式,实现拾起芝麻“抓住小项”;300万吨/年柴油加氢“胆大心细”,开启“双机运行模式”,创造性地将催柴掺炼比例由13.40%提高至24.33%,实现柴油系统“3变2”,120万吨/年柴油装置停工,降低柴油系统营业动力费。通过以上措施,实际增效1524.38万元,确保吨油燃动成本控制在50.9元/吨以内。
5. 控制固本,降本增效
传统印象中,固定成本具有约束性,酌量性占比低,降低固定成本有难度。炼油运行部克服畏难情绪,控制固本的方针是“人员增值、停工降本”。“人员增值”就是通过测算各装置全员劳动生产率、“五班三倒”向“四班两倒”转变,逆向倒逼、正向鼓励员工跨岗、跨车间学岗、一人多岗、在岗增值,提升全体员工技能素养,提高单兵创效值。“停工降本”主要着力点是根据2021年加工920万吨原油排产,合理规划120万吨/年重催、烃重组、润滑油系统的开停工时间节点及生产周期,做到高效高产、开满开优的同时,每月动力盘点结束后对营业外动力消耗进行全面、横向、纵向分析,并利用每月经济活动分析会进行如实通报,力争合理压缩停工待料装置非必要动力营业外支出,降本增效预期2900万元。
6. 制造对账,固本增效
在推行全面预算管理全面对账的过程中,发现在日常生产管理中,对部分炼油业务存在管理盲点和短板,尤以制造费用为甚。制造费用作为固定成本费用中关键的一部分,项目较为繁杂,炼油运行装置采取的措施主要是将该项费用全面打开、全面对账。
综上图4所示,结合目前财务处制造费用及固定成本费用统计结算的实际情况,炼油运行部控制制造费用主要着力点为控制固本动力费及管控排污费,以上两项费用9月合计占固本费用23.23%(全年指标占比23.3%)。同时,需要将关注质检部试验检验费(9月占比3.64%,全年指标占比4.22%)的分配方案,要求其费用分配方案必须具有时效性。排污费管控措施是环保装置环保三剂按照消耗定额,科学按需加注,从源头控制好各装置生产污水排放总量;持续管控好烷基化、两酸以及环烷酸装置废渣出厂量,做好固废减量化,通过以上管控措施,增效1154.51万元。
(三)以创新为驱动,开辟新的效益增长点
把创新作为应对严峻形势的有效法宝,通过对标对表、整合优化、技术攻关,开辟新的效益增长点降成本。
1. 对标先进找差距。以对标先进为抓手,以经济运行分析为平台,从思想、管理和技术分析入手“解剖麻雀”,加强成本费用分析,形成常态例会制,对成本费用的完成情况、效益进度进行跟踪,寻找降本减费空间。为更好地提供精炼每滴油、细算每笔账的数据支撑,炼油运行部将各项成本费用进一步细化和打开,找出影响因素进行改进,制定刚性提升目标,采取目标倒逼机制促使全力降低成本。
2. 管理创新提效能。在设备使用效能上想办法,在两套催化装置,按同类型设备运行的相关性,梳理出管理标准,在设备的缺陷管理,预防性维护、预防性维修等各类运行工况中实现互通互联、数据共享,对提升工作效率、管理减负、共享信息起到重要作用。积极开展平库利库、修旧利废等工作,想方设法减少支出、降低成本。利用日常检维修费用平库266笔,节约成本1099万元,修旧利废完成156项,节约成本1954万元。在非生产性支出上,抓住管理创新这一推动力,办公用品由“每季发放”向“按需发放”转变,办公家具由“整体更换”向“局部更新”转变,资料归档由“纸质归档”向“数字化”转变,大幅减少办公耗材,办公费用同比下降8.3%。
3. 运用技术解难题。针对11套装置长周期运行中的难题,成立催化裂化、连续重整及芳烃抽提和加氢3支装置技术攻关虚拟团队,针对24项难题开展攻关。运用新技术、新工艺优化调整炼油结构,压减成品油,提高“控油增化”能力,通过300万吨/年重催装置增上顶循脱氯等2项技措实施,提高顶循油氯离子脱除率,从根本上解决了催化装置分馏系统的结盐,大幅缓解了柴油加氢高压换热器的结盐状况,也为国内同类装置新技术的快速应用积累了经验。
(四)以降本为目标,凝聚全员同发力
炼油运行部牢固树立系统思维,站位大局,不舍微末,形成单位与个人紧密衔接、一体化统筹的降本格局。
1. 抓住系统这个全局,系统降本。炼油运行部通过打破传统观念和局限,从全局的角度考虑问题,努力向系统思维要效益。牺牲装置发电指标,主动承担起公司炼油区蒸汽系统的平衡任务,通过量化控制指标、优化运行工况,减少重催装置四机组汽轮机用汽量,保供炼油区中压蒸汽,成功实现了动力厂锅炉房单炉运行的“一炉一线”目标。
2. 抓住班组这个关键,深化经济指标核算。班组作为企业组织生产经营活动的基本单位,是企业最基层的生产管理组织。炼油运行部紧抓班组运行这个关键所在,利用新一代信息技术开发的TM平台,实现实时数据库、LIMS、MES、巡检等系统数据的有效集成,为全面开展车间精细化管理提供数据支撑;将成本指标转化为技术指标,技术指标再次转化为操作指标,为开展班组精准操作提供考核依据,通过双向激励促进班组层面严格落实“算细账、细算账”成本理念。
3. 抓住全员这个法宝,开展一人一手一点子活动。成本的执行者是员工,只有调动起广大员工的积极性和创造性,员工才能自觉地节约,尽自己最大的努力为企业创造效益。
(五)以绩效为抓手,形成降本支撑
1. 精准化定标。围绕全要素成本,在绩效考核中相应增加成本管控、计划执行等内容,根据前期试点情况,调整了部分考核指标及要求,形成了“7+1”指标模式,分别是财务指标、生产技术指标、产品质量、安全环保、长周期运行、现场管理、党建管理7个模块和1个否决项指标,考核指标由原来的432项调整至624项,部分考核指标根据生产变动、季节变化进行动态管理。
2. 立体化考评。将管理考核方式优化为“月统计、月考核、季分析、季评比”,各专业组每月对区域指标完成情况进行统计考核,将炼油综合能耗等关键指标分级管理考核,并将指标分解落实到个人,实现连带考核,每季组织一次评比、开展一次情况分析,对于重点难点项目,由各专业主管领导牵头成立攻关组,列入年度攻关计划。完善激励考核机制,有效激发员工的内在动力,推动形成干多干少不一样、干好干坏不一样的鲜明导向。
3. 差异化考核。优化正负激励机制,季度公布评比结果,实行刚性考核,对指标完成优秀、排名靠前的单位,划拨厂长奖励基金对其进行正激励,对于指标完成较差的单位进行考核。同时,将评价结果作为干部提拔、任用、调整的重要依据,对推进工作不力的车间党政主要领导进行约谈,并将评价结果作为评选先进车间的重要依据。
四、实施效果
通过炼油全要素成本管控体系的建立与实施,炼油运行部找准了降本路线,在提质增效方面取得了新的突破,形成了全员齐参与、算细账、强攻关的“一盘棋”局面,逐渐消化了内外部环境的不利影响,在顺利完成安全生产年度目标的基础上,超预期完成了挖潜增效目标,以高效率、高效益推进了高质量发展。2021年挖潜增效1.3亿元,完成目标值的190.28%。
一是成本费用显著降低。2021年,炼油完全加工费201.21元/吨,在26家炼油生产企业中排第5名,比板块平均水平258.70元/吨低57.49元/吨,排名比上年同期上升1名;现金单位加工费为125.15元/吨,较财务预算134.0元/吨大幅下降8.85元/吨;吨油辅材12.54元/吨,较财务预算15.39元/吨降低2.85元/吨;吨油燃动49.62元/吨,较财务预算50.90元/吨降低1.28元/吨;吨油添加剂为0.40元/吨,较财务预算0.65元/吨降低0.25元/吨;固定成本费用为63649万元,较预算64804万元降低1154.51万元。
二是技经指标稳步攀升。炼油综合能耗、原油加工损失、单位辅料费用等关键技经指标创历史最好水平。轻油收率、目的产品收率、催化丙烯收率、95号及以上汽油比例等4项指标提升,分别同比提升0.84%、0.48%、0.23%、8.79%;原油加工损失率、炼油综合能耗、柴汽比、单因数耗能、吨油耗新鲜水等5项指标降低,分别同比降低0.03%、1.17千克·标油/吨、0.09、0.17千克标油/吨因数、0.01 吨/吨。
三是创新成果不断涌现。炼油运行部员工积极解放思想,打破常规,成本管控意识不断强化,孵化出多项技术创新成果。2020年至今,成功开发了PX级二甲苯、100LL航空汽油、UL91无铅航空汽油和100vLL低铅航空汽油4项新产品,拓宽了产品销路,达到降低生产成本、完善产品结构“双赢”目标。通过技术应用和考核机制创新,固废同比下降85%,回炼废油6500吨,增效达千万元。
四是管理效能显著提高。通过低成本管控,炼油运行部形成了以市场为导向、以效益为中心,对标先进指标,优化资源利用的工作方法,实现了资源向最佳加工路线配置;对标管理实现了由表观指标对标转向管控方法、管理工具、管理策略的对标,基层单位向管理极限挑战、向对标要效益的主动作为意识显著提升,基层员工主动建言献策的热情被充分激发;管理专业技术人员的工作方法开始由浅层事务型向深度专业型转变,超前思维能力逐步养成,实现了管理上水平、技术上水平,原炼油厂荣获兰州石化2021年度“先进单位”称号,炼油运行二部荣获2020—2021年度集团公司“装备管理先进集体”称号。
成果其他创造人:臧艳妲 赵 静 王建红 姜长双 朱玉新 高志成

735
点击量
7
下载量
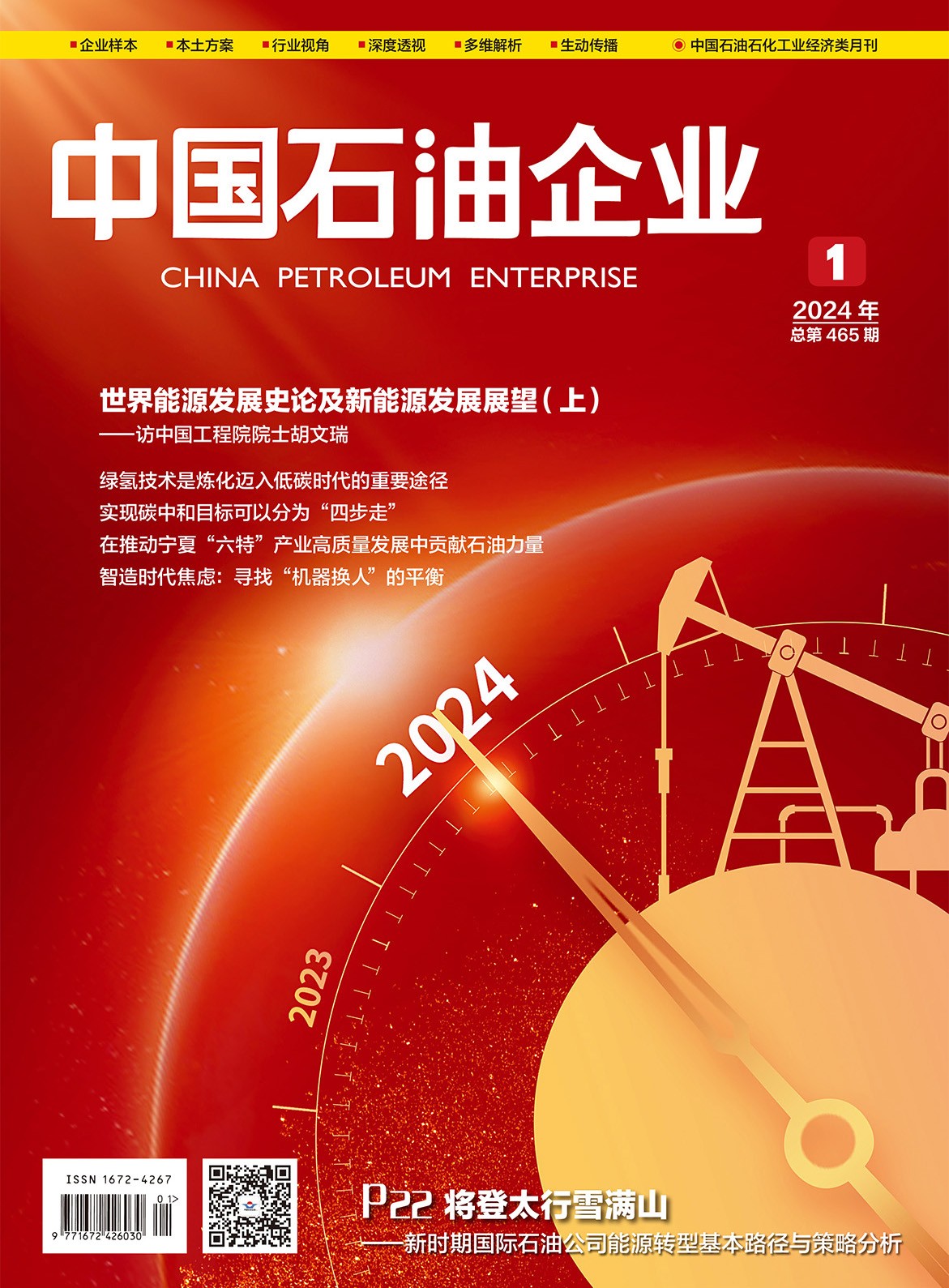
刊出日期:2024.01
主管单位:中国石油天然气集团有限公司
主办单位:中国石油企业协会,中国石油企业协会海洋石油分会
国际标准刊号:ISSN 1672-4267
国内统一刊号:CN11-5023/F
国外发行代号:M1803
国内邮政编码:100724
广告经营许可证号:京西工商广字第0433号(1-1)