2021年5月,中国石油集团公司董事长戴厚良到川渝地区调研,对四川石化提出“率先打造世界一流炼化企业”的目标。为深入贯彻落实集团公司党组关于四川石化公司打造大检修标杆示范工程的指示精神,以实际行动落实好“全生命周期精益化大检修”管理理念(简称精益化大检修),公司坚持“八分准备、二分实施”原则,优化顶层设计、强化总体布局、细化战术安排、固化样板先行、深化数智赋能,坚持“高标准启动、高水平实施、高质量验收”原则,通过理论创新、思路引领、实践探索,保证各项工作按照总体统筹有序、高效、准点完成,最终实现精益化大检修既定目标。
超前启动实施,扎实统筹推进,高标准做好检修准备
一、全面畅通大检修工作推进机制
1. 成立大检修组织机构。公司于2021年4月成立了“1+14+11”的大检修组织机构。设立1个大检修指挥部,负责大检修指挥部全面领导;在机动设备部设立指挥部办公室,负责贯彻落实指挥部各项决策及部署。在公司机关设立检修协调、开工停工、安全环保等14个职能小组。在二级单位设立11个分指挥部,具体组织实施所属装置检修工作;结合公司领导及机关各处室中层干部任职经历,施行检修装置包保,定期深入现场检查、参加检修会议、协调推进大检修各项工作。
2. 建立大检修体系文件。按照组织机构以及职能小组分工,2021年11月25日工作小组发布了公司《大检修管理手册》,作为公司大检修管理的最高级别指导性文件。明确了各职能小组(各处室)、分指挥部(各生产部)、施工单位职责分工,组织制定了《大检修质量管理手册》等11项体系文件,最终形成公司层面的管理体系。
3. 绘制大检修任务蓝图。按照总部要求节点,倒排工期,编制《四川石化公司大检修准备工作总体统筹》,作为公司大检修作战时间表,涵盖大检修例会安排、大检修计划、招标选商、长周期物资采购、同步实施技改项目、开停工安排、承包商对接、机具人员到厂等关键环节,均按月列出时间安排。2022年5月按照《炼化企业大检修管理指导意见》,详细梳理出80项具体工作的时间节点,再次优化完善了《总体统筹》。每月执行时,再细化到每周进行具体安排。
4. 畅通工作协调推进机制。公司建立“里程碑大会—大检修例会—专项对接会”三级会议体系,明确每次会议主题、参会单位、会议频次及时间,结合检修工作进展,按期召开各级会议,先后召开大检修启动会、动员会、誓师大会等里程碑大会6次,公司级大检修例会53次,计划、检修、方案、物资等各专业对接会94次,安排部署大检修工作,协调问题,逐级深入推进,确保大检修各项工作高标准、高质量完成。结合检修工作进展,大检修指挥部明确每次会议主题,会上安排4个监督单位、14个职能小组(不按照处室)依次进行汇报,检修协调组通过大检修信息化平台每日通报各职能小组、施工单位工作进度、质量、自主管理、考核、人员等方面存在的不足,协调当前存在的问题。
二、坚持准备工作“早启动、守节点、严把关”
1. 开展大检修“回头看”工作。按照2020年12月炼化公司“设备制度落实主题月活动”、2021年2月炼化公司下发的《炼化企业大检修“回头看”工作总结》、2021年5月下发的《加强炼化企业大检修工作相关措施》等要求,对照近年来发生的典型事故事件和共性问题,公司深入开展2018年大检修“回头看”工作,对上轮大检修进行了认真回顾和思考,重点从工期制定、大检修准备、检修单位选择与标段划分、停开工过程管控、施工过程管控、费用控制、同步技改项目等方面,系统查找安全、质量、进度管控存在的不足,梳理装置长周期运行瓶颈问题13项,逐项查找差距,分析原因,制定相应整改措施及应对方案。在装置停工前24个月,组织梳理装置长周期运行问题清单,完成《装置大检修技术方案》编制。
2. 做好设备运行末期状态评估。按照炼化板块下发的36项隐患排查要求,应用状态监测、腐蚀监测、涡流扫查、红外热像、RBI风险评估技术,并结合企业自身特点以及同类装置事故教训,主动深入开展涡流扫查等专项隐患排查41轮,对异常部位进行扩大排查,提前检查发现问题6770项,持续优化大检修计划、方案,切实做到“应修必修不失修,修必修好不过修”。
3. 科学编制大检修策略。公司按照《炼化装置大检修规范化管理100条》,以及《炼化企业大检修全生命周期KPI考核评价体系实施细则》,组织制订《四川石化公司2023年大检修策略》,涵盖动设备、静设备、仪表设备、电气设备、防腐土建等五个专业。按照“一装置一策”“一机一品一策”,组织各分指挥部结合每个装置个性化特点编制《装置检修策略》《机组检修策略》,为检修项目立项、检修计划编制提供科学依据。
4. 严肃大检修计划立项。提前30个月启动大检修调研和计划论证工作,开展检修计划论证4轮,精准预判常压塔顶部塔盘严重腐蚀等多项隐蔽工程重大缺陷问题,修复方案及措施得到提前安排部署,避免了检修被动局面。
三、精选大检修队伍,严把分包队伍关,是本次大检修成功的关键
1. 制定方案。停工前2年启动大检修队伍调研工作,通过检修现场调研、板块外审交流等方式,深入了解潜在队伍的业绩、行业口碑,为选商方案制定提供准确依据,提前排除能力弱、口碑差的承包商。合理划分检修标段,合规制定选商方案,减少界面划分,提高检修效率,降低检修成本。按照“专业人干专业事”的原则,科学、合理划定专项检修项目,将乙烯保冷修复、PX转阀检修、无氧装卸剂、化学清洗等业务纳入专项检修项目,借助专业力量实施专业检修,保障检修质量和检修效率。
2. 精选队伍。督促中标单位尽早落实作业队、分包商,逐一调研作业队和分包商的人员构成、业务能力和行内业绩。对业务能力弱、业绩不良的作业队和分包商直接拒绝入场,从源头把控参检人员的业务及安全履职能力,为大检修顺利完成打下坚实基础。
3. 管理前置。联合政府执法部门深入参检员工食堂、住宿点,开展食品、住宿、通勤、用电用气安全等专项检查,确保员工吃得放心、住得安心。倡导“一家人、一条心、一起干”的管理理念,提供现场标准化休息场所,按期支付大检修预付款,开设大检修会议茶点,开通柴油车现场送油服务等,以实际行动服务参检单位。设立24小时大检修热线电话,随时为参检员工提供检修咨询、薪酬发放争议的协调等工作,解决参检员工的后顾之忧。
4. 过程监督。及时约谈表现不佳的参检单位项目经理,督促参检单位主要领导到场坐镇指挥;直接清退表现不佳、安全管控不良的分包队伍;会同第三方质量和安全监督人员开展现场不间断巡查,及时纠正质量问题和不安全行为,奖惩结果通过大检修平台实时公开、透明展示,提高了参检队伍比、学、赶、帮、超的积极性,不仅有效提高了检修效率,还助力承包商降低用工成本。由于本次大检修队伍选的较好,经前期反复多次对接,做到了心中有数,现场作业忙而不乱,除换剂、探伤等作业外,基本实现了正常的作息安排,员工整体精神面貌良好。
5. 后评价应用。组织开展大检修劳动竞赛,通过大检修平台实时展示各参检单位量化得分排名,激发参检单位及员工的积极性和创造力。表彰优秀承包商14家、供应商19家、服务商18家。表彰承包商先进个人144人。对违章较多的单位,进行黄牌警告;对排名靠后的承包商,直接末位淘汰。
四、开展重难点项目桌面推演,积极采用新技术,高效完成大检修准备
大检修指挥部结合现场实际情况,制定了桌面推演计划,聘请第三方质量、安全监督单位对催化装置外取热器管束更换、乙烯三机组检修、芳烃吸附罐更换、火炬检修、挤压机组检修等重难点项目开展10轮桌面推演,充分发挥专家作用,通过方案审核和现场指导相结合的方式,分析时间、空间上的交叉作业,检修难点、方案缺项、技术难题等,及时发现问题,提出整改意见,逐项补充完善,提前预判检修程序不确定性,提高参战各部门管理人员的统筹协调能力,提升检修过程中面对难题的应变能力,确保检修顺利完成。
创新组织模式,强化过程监督,高水平实施检修管理
一、扎实开展承包商安全自主管理是本次大检修安全管理的关键
1. 建立清单。建立承包商自主管理检查清单,明确承包商安全目标、准入资质、教育培训、人员资质、应急管理、隐患排查、检修进度、机具设备等9个方面24项管理内容,明确每项内容自检频次及要求。
2. 汇报剖析。每日大检修例会上,随机抽选一家承包商进行单位自主管理汇报,自我剖析检修进度、质量和安全管理存在的不足及下一步改进措施。
3. 检查考核。成立联合检查组,对承包商自主管理情况开展专项检查,进行奖惩兑现,有效推动自主管理。
4. 共同提高。通过实施承包商自主管理,提高了大检修质量、安全、进度管控能力,体现一家人、一条心、一起干的管理理念。
二、持续筑牢环保管理底线
1. 固废即产即运。提前选定大宗废剂处置厂家,实现PX装置吸附剂、渣油加氢装置催化剂卸出后即卸即运,消除现场着火自燃的风险。
2. 废气达标监控。优化加热炉控制,精准控制炉膛氧含量,制定超标应对措施,实现废气有序排放,开停工期间24套废气在线监测仅出现12小时均值超标。
3. 异味有效管控。在481装卸车单元、420罐区、422罐区、丁辛醇装置和轻重污油装置引进5套移动式VOCs治理设施,实现挥发性有机物达标排放。
三、深化责任落实,全面实施大检修工作包管理,实现检修标准化、规范化
1. 构建工作包管理模型。确定“装置—工作包—单台设备”三级管控,实行“设备工作包+专业工作包”矩阵管理,明确“组织协调、管控矩阵……”等11项管控内容,形成点面衔接、相互关联、自主管理的工作流程,最终实现检修过程数据、表单、流程信息化、规范化管理。
2. 畅通工作包作业流程。结合业务实际需求,形成工作包搭建及业务管理流程,为精益化大检修工作包具体实施提供了清晰的工作思路。
3. 完善工作包基础数据。发挥基层力量,组织二级单位成立工作包模板编制小组,制发23个设备工作包模板,统一了工作包编制、管理流程及业务要求。组织各单位编制工作包450个、信息表单4950份,为实现“不同的人干同一件事,遵循同一流程、按照同一标准,得到同样的结果”奠定了基础。
4. 创新工作包进度指标体系。建立“项目→工作包→装置→生产部→公司”逐级统计模型;首次提出“综合完成率”“节点完成率”两类进度指标;通过综合完成率实现检修进度纵向统计,通过节点完成率实现关键节点横向统计。
5. 重塑大检修方案管控体系。按照分级管理、逐级细化的原则,构建公司、生产部、施工单位等各方大检修“总体→专业→专项”三级管控方案体系,作为大检修管理体系文件。按照炼化板块关于精益化大检修的有关要求,公司发布统一的方案模板,大检修指挥部编制《大检修管理手册》,各职能小组编制公司级《大检修专业管理手册》,各分指挥部编制《生产部装置大检修技术方案》《专项管控方案》,施工单位编制《施工组织设计》《专项施工方案》,最终转化形成《大检修工作包》和《日工作清单》,通过向下逐级细化方案,压实各层级工作责任,确保各阶段工作任务PDCA闭环落实。
6. 科学制定各级施工统筹。以工作包为基础单元,按照“主线项目工作包统筹→次主线项目、重点项目工作包统筹→装置停检开统筹→装置施工网络统筹→公司总体施工网络统筹”顺序,按照发布统筹模板,逐级编制大检修施工统筹。
7. 高效开展工作包物资管理。将ERP物资供应全过程数据集成到大检修平台,实现“订货率、到货率、领用率”自动统计,各级人员可实时掌握大检修物资的订货、入库、领用数据,实现工作包物资保障及全流程管理;强化库房物资“验、收、存、发”标准化管理,制定《停工检修物资保供方案》;实现停工前物资到货率97%,降库金额5649万元,降库率21.54%,资金节约率12%;优化项目统筹,各类大型设备、三剂等物资根据项目进度直达现场,避免二次倒运。
采用“网格化+专业化+标准化”的管理模式,进一步强化检修管理责任
一是建立公司领导及机关各处室中层干部检修装置包保责任制,专业工程师和40名安全监理、40名质量监理人员,按照“区域+专业”进行网格化分工,“定格、定人、定责”。二是邀请兄弟企业专家到现场开展催化两器隐蔽问题检查,对催化衬里、无氧换剂、大型机组、保冷修复、化学清洗等开展专业化检修,确保检修质量、安全管理全方位受控。三是打造乙烯三机组检修、换热器集中清洗试压等8个样板工作,通过样板引领现场标准化检修。
样板工程一:换热器管束集中自动化清洗。公司按照“功能区块明确、工作界面清晰、油污废物集中、设备转运便利”的原则,建成施工面积7500平方米,管束存储能力120台的标准化、定制化清洗场地,引入先进的高压水自动清洗设备,对全厂24套装置462台浮头式和U型换热器管束进行集中清洗,同步完成160台管束集中试压、281台管束涡流扫查,通过大检修平台实行送洗预约、APP质量控制确认、进度自动统计,实现换热器管束集中清洗—涡流扫查—集中试压高效开展。
样板工程二:关键机组标准化检修。打造“装置现场、精修厂房”两个标准化作业阵地,从桌面推演、现场布局、成品保护、作业过程管控四方面着手,实现“人员培训专业化、现场布局合理化、成品保护规范化、过程管控标准化、质量验收信息化“,做到检修过程有条不紊、检修作业忙而不乱、检修管理从容不迫。
一、数字驱动赋能,管理方式变革,高质量完成检修目标
1. 开发大检修信息化平台,实现大检修信息管理。
结合工作包11项管理要素,综合检修计划、ERP订单、物资管理、门禁系统、承包商管理系统数据信息,自主开发大检修信息化平台,实现各系统数据集成管理、统计,各级管理人员通过平台能快速、直观查看不同阶段关键统计信息,提高管理效率。
2. 借助大检修平台手机终端APP,实现检修工作包落地执行。
以工作包“管控矩阵”为标准,开发APP应用,为平台提供底层数据支持。利用公司5G专网,参检人员通过手机APP,快速进入工作包任务清单,录入检修数据、上传影像资料,通过短信提醒推送功能,实现工序验收自动衔接。检修人员按既定流程对检修质量步步确认,管理人员按照分工进行验收。检修数据实时上传云端,实现检修进度自动统计、检修记录自动形成,保证检修记录真实准确。属地单位与第三方质量监督单位、施工方共同组建质量监督团队,开展工作包自主管理执行情况监督和检查。
3. 以工作包为核心,设计进度统计模型,实现准备阶段、实施阶段进度自动统计。
准备阶段:重点对“人、机、料、法、环”等要素开展进度管理,系统不仅实现了方案、统筹、工作包分级管理、线上审批,而且还可以自动统计准备阶段不同月份各要素进度情况,各级管理人员可通过平台实时掌握大检修各要素准备情况及预制、预搭项目进度。
实施阶段:重点对工作包、装置、部门、公司的综合完成率、节点完成率进行监督。检修人员通过手机APP进行步步确认后,平台能同步统计各工作包执行情况,各级管理人员通过综合完成率进度情况,开展针对性的纠偏工作。
在实施阶段同步建立各装置主线项目、重点项目里程碑节点图,与工作包完成进度、DCS工艺参数自动关联,实现进度节点“红绿灯”自动展示。各节点完成数据自动纳入属地单位、参检单位大检修劳动竞赛,得分排名在平台实时展示,形成了良好的比、学、赶、超竞赛氛围。
二、推进技术攻关,提升装备性能,高回报实现检修价值
1. 全面推进国产化攻关,实现科技自立自强,解决部分关键装备“卡脖子”问题。
通过统筹协调、上下联动、跟踪督导逐级压实责任主体,积极推进国产化攻关,缩短了物资采购时间,节约了检修费用,彻底解决了一大批关键装备卡脖子问题。一是坚决贯彻落实集团公司《重大技术装备推广应用实施意见》要求,推进集团公司首台(套)重大设备技术应用,在国内率先实施烟机入口蝶阀(DN1650)国产化应用。二是锚定装置长周期运行瓶颈问题,采用国产缠绕管换热器替代重整进口板换,替换后换热效率得到有效提升,大幅减低每年燃动费用。三是裂解气大阀配件、汽轮机配件等国产化,长周期备件供货周期减少约60天。四是坚持降费增效,顺利完成进口变频器、重整还原气加热器国产化替代(电加热器价格仅为进口设备的20%)。五是坚持问题导向,完成炼油火炬、污水厂反渗透装置进口PLC系统国产化替代,保证装置安全平稳运行。
2. 优化装备性能,大力开展节能减碳,助力企业高质量发展。
以高质量发展为目标,以稳定创效为中心,以精细化管理为主线,围绕“深化节能减排,推进高质量发展”主题,大检修期间坚持“三个结合”,实施了一大批节能减排项目。一是将节能减碳与行业先进对标相结合,扎实开展形势政策教育,积极推进能效达标和减碳工作,完成乙烯装置裂解炉新型高效节能炉管替代和催化装置余锅蝶阀改造,生产成本大幅降低。二是将节能减碳与生产瓶颈治理相结合,完成PX抽余液体塔盘改造,改善分离效果,大幅提高生产效率;实施芳烃异构化循环压缩机组性能瓶颈改造,每年节约成本300余万元。三是将节能减碳与隐患治理相结合,积极推进炼油区加热炉4台空气预热器升级改造,加热炉热效率显著提高;完成乙烯装置保冷修复工程,丙烯压缩机组高压蒸汽明显降低。
取得的成效
一、管理效益
四川石化深入贯彻集团公司党组领导关于“打造四川石化标杆示范工程”的现场指示精神,严格落实精益化大检修理念,精选大检修队伍、优化停检开统筹、推行工作包应用、创新大检修平台、强化承包商自主管理,带领广大干部员工靠前指挥,扎根现场,统筹协调,解决困难;全体员工中秋、国庆和周末假期全程无休,同舟共济、攻坚啃硬,最终带领113家参检单位10067人,历时55天圆满完成44套生产装置及单元14项投资项目、6504项检修任务,17项指标圆满完成,项目验收一次合格率100%、装置按期交工率100%、装置一次开车成功率100%,实现了“零事故、零污染、零伤害”目标,夺取了“大检修决胜战”全面胜利,实现“安全、环保、优质、高效,一次性开车成功”大检修总体目标。
二、经济效益与社会效益
通过精益化大检修探索实践,四川石化公司各项成本费用大幅减少。
大检修全生命周期管理得分2343.93分,在当年中国石油9家大修炼化企业中排名第一,成功创建“大检修标杆示范”工程,荣获“集团公司设备管理先进单位”。在大检修期间,来自中国石油、中国石化、中国海油的10余家炼化企业到四川石化公司观摩学习。公司后续多次受邀赴行业、各企业讲授精益化大检修管理实践,为国内炼化行业提供了可推广、可借鉴、可固化的经验参考,已然成为四川石化推动世界一流炼化企业建设的响亮名片。

688
点击量
2
下载量
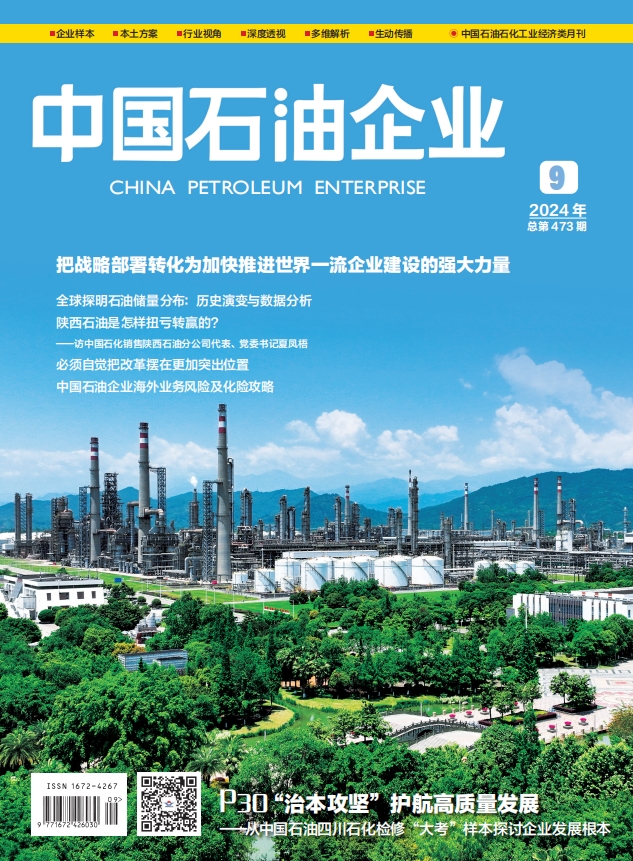
刊出日期:2024.09
主管单位:中国石油天然气集团有限公司
主办单位:中国石油企业协会 中国石油企业协会海洋石油分会
国际标准刊号:ISSN 1672-4267
国内统一刊号:CN11-5023/F
国外发行代号:M1803
国内邮政编码:100724
广告经营许可证号:京西工商广字第0433号(1-1)