摘要:本文重点分析输油管道在埋设施工后,受到土壤侵蚀而引发的严重事故,以及目前的防腐蚀管理措施;通过深入调查研究,了解土壤腐蚀原因、腐蚀措施,并结合不同影响因素分析,明确科学防腐蚀管理及措施,以更好地提升防腐蚀效果。
关键字:输油管道;评价系统;腐蚀;防护
对于石油企业来说,其油气及其制品运输形式是靠物体在管道内顺着压力方向循序移动实现的,与其他运输方式的重要区别在于管道设备是深埋地下且静止不动的。因而,深埋地下的管道在投入使用后,容易受到很多外部因素影响,比如温度、压力、地理条件、微生物,容易导致管道发生损坏的问题。油品输送阶段,埋地钢质管道容易受到土壤环境影响,但是这些管道检修、维护管理的难度较高,需要投入大量资金,同时也隐藏着巨大的安全隐患。埋地钢质管道的土壤环境侵蚀严重,腐蚀问题加剧,一旦腐蚀后发生穿孔情况,将会导致油品泄漏,引发环境污染乃至爆炸事故,危害人们生命安全。
1 土壤腐蚀影响
1.1土壤腐蚀
土壤内含有大量的水、空气,而水中含有盐类物质,这些物质的存在使得土壤具备导电性。而且土壤的物理性质、化学性质会因为季节、水位等变化而产生变化,加上植被根茎的持续影响,使得土壤电化学性质不稳定。这样的情况下,土壤周边会存在腐蚀性环境,随着时间的延长,腐蚀也会加重。
1.2微生物腐蚀
有些土壤内含氧量比较少,也有可能存在微生物的腐蚀管道情况,比如细菌让水中的盐变化为可溶性硫酸盐,受到该物质的持续侵蚀,管道发生氧化反应,转变为氧化物,从而发生腐蚀问题。
1.3电流腐蚀
钢质管道形成腐蚀的原因还有电流腐蚀,尤其是杂乱电流的影响,其可以使得水内的离子经过电解反应,逐步和铁发生反应,从而导致管道发生腐蚀的问题。电流腐蚀的特性是集中性强,经过调查发现,我国的土壤腐蚀速率可以达到1mm/a以上,同时受到杂乱电流、微生物的腐蚀作用,容易出现管道穿孔问题。因此,必须选择防腐蚀措施,保证管道运行的安全性。
2 输油管道防腐措施
2.1输油管道安全问题
2.1.1输油管道腐蚀
将输油管道埋设到土壤内,因为土壤中各种物质的影响,防腐层逐步的老化,加上一些不法分子盗窃油品,出现了管道严重损坏情况,进而引发严重的腐蚀问题,影响石油输送的安全性。
2.1.2管道低输量运行
我国开采的原油主要特点是高含蜡、高粘度、高凝点,所以造成传输的难度较高。在油品的输出量较少的情况下,黏度的增大会带来能耗升高,而低温则会引发凝管事故风险。
2.2输油管道腐蚀控制问题
2.2.1管道建设时质量控制
管道在建设初期,要进行全面的勘探,了解管道的走向,加强现场检查,禁止使用存在质量问题的管道。
2.2.2管段腐蚀与控制
要想全面提升管道的质量,加强焊接质量管控极为重要。管道焊接部位比较薄弱,受到伸缩、电位、热应力、蠕动等影响,焊接部位极易出现缝隙。地下水经过缝隙进入到管道内部,进而导致腐蚀问题的发生。为了防止这一问题的发生,在套管内插入管道时,应该在两侧使用沥青等介质密封处理。
2.2.3废旧管材研究
为了保护生态环境,重视废弃管材的回收利用。对废旧管道的腐蚀情况展开调查,评价管道内外腐蚀因素以及危害性,总结出合理的应对措施。对管道输送液体、环境进行调查,综合评估管道缺陷的问题,提出具体的防腐蚀措施,保障管道的安全性。
2.2.4定期检查和校验
定期对管道进行检查,校验腐蚀性参数,落实防腐检查与检测工作。防腐体系包含的内容较多,比如防腐材料选择、防腐方法选择等,以确保防腐蚀效果合格。为了将腐蚀影响控制在最小范围内,应加强管道参数的调查分析,了解腐蚀力学寿命条件,并根据我国的国家标准展开定期的评价。
2.3输油管道防腐主要措施
土壤腐蚀中包含电化学腐蚀、杂散电流腐蚀等,所以应该对土壤腐蚀情况展开全面深入的调查,了解管道的性质,根据环境、物化性质分析,以满足管道防腐蚀的要求。具体来说,输油管道防腐蚀措施如下:
2.3.1管道内外壁防腐
钢质输油管道埋入地下后,形成腐蚀的原因较多。我国在20世纪50年代之前,使用石油沥青、煤焦油等进行管道防腐蚀处理;20世纪60年代应用塑料管道保护套管;70年代使用复合材料进行防腐蚀处理,比如聚乙烯、环氧粉末等,达到防腐、绝缘的效果,材料强度也得到提升。经过以往经验总结,使用红丹油防锈漆等作为底漆,涂抹到管道的表面达到腐蚀的效果。同时,加入汽油或者煤油0.0056左右,可以达到防锈性能提升的效果。当前我国在管道的防腐蚀处理中,复合型的试剂包含咪啉类缓蚀剂和复合型缓蚀剂,这些材料的防腐蚀性能都非常好,完全可以满足防腐蚀的要求。与此同时,很多单位都会选择多种防腐蚀的方式,提高综合防腐的效果,延缓管道腐蚀,促进管道寿命延长。
2.3.2内涂层
为了延缓腐蚀的速度,保证管道运行的效果,通过管道内涂层的方式进行防腐蚀处理,提高管道的防腐蚀性能。管道内涂层可以有效的阻隔腐蚀介质和管道的接触,同时还能提高光洁度、降低摩阻与成本。内涂层的材料可供选择的范围比较大,制造工艺也比较简单,且总体成本比较低。目前我国的管道内涂层应用热喷玻璃防腐工艺比较常见,耐腐蚀效果提升比较明显,将碳钢与酸性气体隔离。为了更好的利用废旧管线,内涂层应用环氧涂料的内涂方式,进行管道进行返修处理,提高资源的利用率。通过分析发现,内涂层的防腐蚀技术可以延缓管道的腐蚀,综合利用价值非常高。
2.3.3外涂层
外涂层是重要的防腐方式,目前我国的管道外涂层防腐蚀比较多,比如FBE防腐层、三层PE防腐层、环氧粉末防腐层、石油沥青防腐层,各种材料的性能和优势不同。石油管道的安装单位对现场进行调查了解,分析腐蚀形成的原因,以确定最为合适的外涂层材料,从而达到管道防腐蚀的效果。
2.3.4阴极保护
阴极保护工作原理是利用发电机产生电流,让性质活泼的材料不会流失电子被氧化,从而保证材料的稳定性,达到防腐蚀效果。为了提高阴极保护的质量水平,达到管线电位的稳定性,使得管道和某些物质尽量保持隔绝性,避免接触。有些管道直接安装到地面,通过使用阴极保护的方法可以实现长期的防腐蚀处理,延长管道寿命。
2.3.5排流保护
埋地输油管道进行排流保护,其主要的工作原理是结合管道是否存在正负性交变,以确定具体的排流方式。如果没有正负交变,则应用支流排流;如果存在正负交变,则应用极性排流;如果情况比较复杂,使用强制排流。比如,管道在使用中,平行段应用排流保护的方式时,应用阴极保护方法以更好地规避杂散电流影响,将电子得失有效控制,从而达到管道良好的阴极保护效果。
2.3.6电化学保护
电化学腐蚀是比较常见的,各种条件下都会出现,所以要使用良好的电化学保护方法。电化学防腐需要使用补充遗失电子的方式进行,使用多种材料进行保护。我国目前对于石油输送管道中使用的防腐方法多数都是通过强制电流保护、牺牲阳极的辅助阴极保护性措施。电化学腐蚀的反应中,低电位金属失电子极易发生氧化的问题。按照目前我国的防腐蚀相关的标准,将管道和电源负极连接,辅助阳极和正极连接,从而可以在管道的周边形成电位差,以实现电流保护的目的,确保管线不会发生腐蚀损坏问题。
3 结语
综上所述,在现代社会发展之下,对于石油资源的使用量不断增多,安装施工的石油输送管道数量也在增加,而钢质输油管道的腐蚀问题却一直存在,极大地影响了管道运行的安全性。因此,结合钢质管道的运行状态,选择合适的防腐蚀措施,总结防腐蚀策略,将为今后石油输送管道的安全通行产生积极影响。

448
点击量
0
下载量
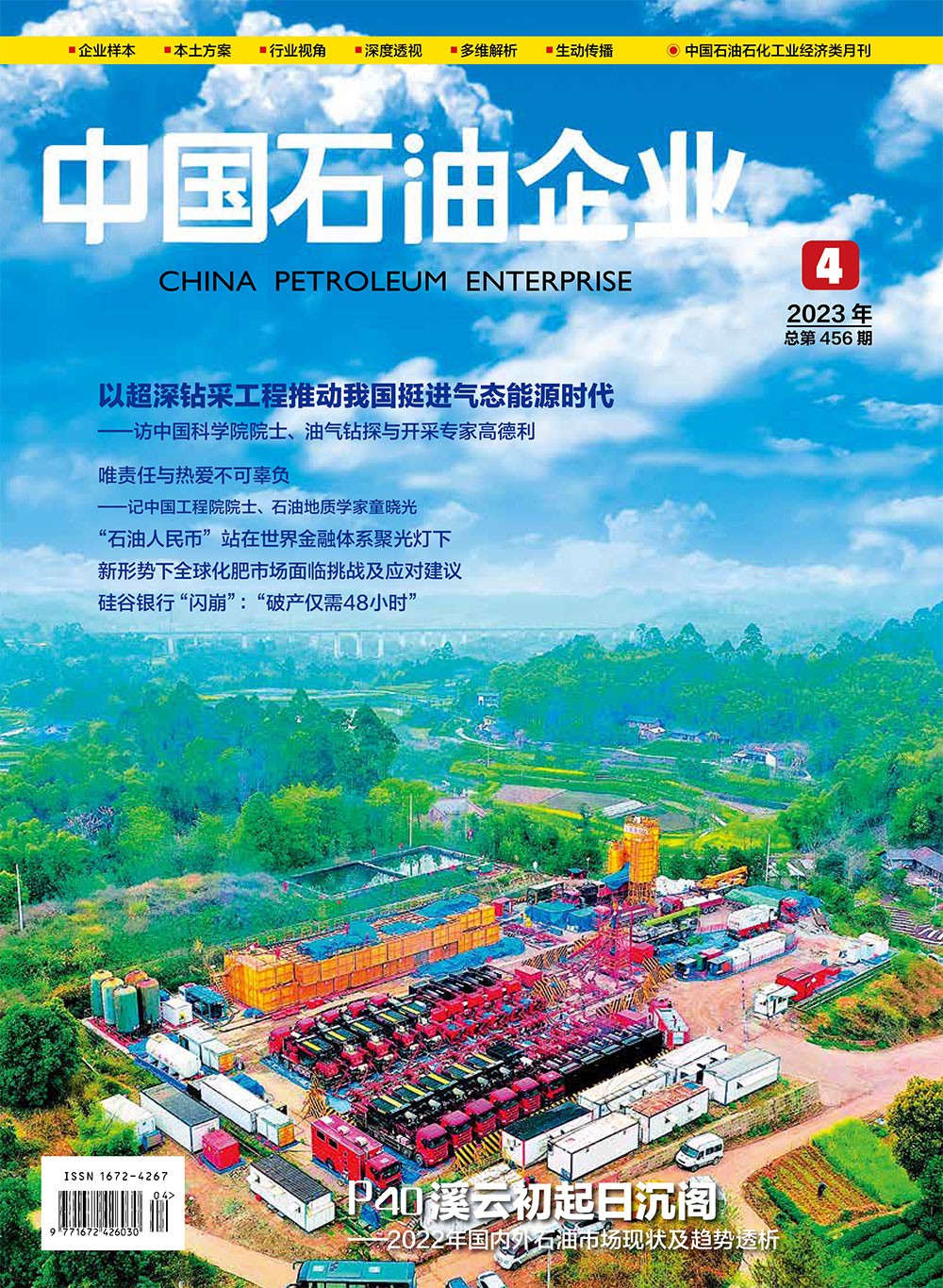
刊出日期:2023.04 上旬
主管单位:中国石油天然气集团有限公司
主办单位:中国石油企业协会,中国石油企业协会海洋石油分会
国际标准刊号:ISSN 1672-4267
国内统一刊号:CN11-5023/F
国外发行代号:M1803
国内邮政编码:100724
广告经营许可证号:京西工商广字第0433号(1-1)