将钻头一寸寸伸向海洋深处
1500米,通常被国际上定义为深水与超深水的分界线。尽管超深水区蕴藏着丰富的油气资源,但深入的每一步都“难如登天”—水深每增加1米,压力、温度、涌流等情况都会发生剧变。一套安装在水下1500米处的设备设施,受到的压力相当于在指甲盖上站了一个体重300斤的人。而且深水开发对技术、装备能力、关键设计指标的要求都极高。国际上只有少数几家大型石油公司具备深水开发技术能力。
中海石油(中国)有限公司海南分公司在“深海一号”建造阶段实现3项世界级创新,运用13项国内首创技术,攻克10多项行业难题,是中国海洋工程建造领域的集大成之作,标志着在星辰大海征途中,中国海洋石油人将钻头一寸寸伸向更深邃的海洋……
通过建设“深海一号”超深水大气田,海南分公司提出了超深水复杂油气勘探的“中国认识”,贡献了超深水大气田有效开发的“中国方案”,建成了超深水大气田作业船队的“中国装备”,定义了超深水大气田工程建设的“中国速度”,打造了国产化设备示范应用的“中国平台”,其百折不挠、自主创新精神值得本刊大力推荐!
“深海一号”超深水气田高效钻完井管理创新与实践
□ 文/刘和兴 孟文波 刘书杰
摘 要: 在国家能源安全形势日益严峻的背景下,为推进中国海油集团“1534”总体发展思路和“十四五”规划实施,全力保障国家能源安全,开发南海深水油气资源势在必行。“深海一号”气田是我国首个自主开发深水气田,区域环境和地质条件复杂,存在“一深一低三高”特点:水深达1547米、海底温度最低2摄氏度、部分区域含浅层气、高投入高风险、高科技,给“深海一号”气田开发安全高效钻完井作业带来极大挑战。中海石油(中国)有限公司海南分公司依托国家级、公司级重大项目提供的支持保障,努力开展技术攻关与管理创新实践,形成了一套包括4项创新成果的深水气田开发安全高效钻完井管理体系,广泛应用于“深海一号”气田开发钻完井工程中,深水钻完井安全性和作业效率得到全面提升,并且实现了我国深水气田的自主开发,共计产生直接经济效益16.76亿元。该成果将推广应用于陵水25—1深水高温高压气田开发钻完井作业、陵水18—1/18—2超深水气田勘探开发,以及南海中南部油气资源勘探开发,为南海万亿大气区建设提供重要保障。
关键词: “深海一号”;高效钻完井;自主开发
中海石油(中国)有限公司海南分公司(以下简称“海南分公司”)是中国海洋石油集团有限公司控股的中国海洋石油有限公司下属的一家境内分公司,总部设在海南省海口市,主要负责东经113°10′以西的中国南海海域石油天然气的勘探、开发和生产业务,拥有4个油气资源盆地:北部湾、珠江口、莺歌海及琼东南。海南分公司下设勘探开发部、生产部、工程技术作业中心、研究院、健康安全环保部、协调部、计划财务部、商务合同部、人力资源部、行政部、工程建设部等18个部门和单位,现有员工2700余人。
通过30多年的高速发展,海南分公司通过管理创新和技术攻关,有效克服了深水、高温高压、北部湾地层易垮塌等一系列钻完井技术挑战,已连续12年油气产量超过1000万立方米,并于2020年成功迈入我国10大油气田行列。“十三五”以来,国家将南海油气开发提高到国家海洋战略高度,海南分公司更加注重海洋油气资源和海洋环境的保护,通过技术攻关与管理实践相结合,形成了一套“深海一号”超深水气田开发安全高效钻完井管理创新与实践方案,助力油气勘探开发步伐向深水、超深水、深水高温高压区域迈进,加速建成“南海万亿方大气区”,切实保障国家能源安全。
一、“深海一号”超深水气田开发安全高效钻完井实施背景
我国南海油气资源量高达350亿吨,约占我国总资源量的1/3,其中深水占比超过70%。我国是世界油气消费、进口第一大国,原油对外依存度超过70%,国家能源安全形势日益严峻。能源安全是关系国家经济社会发展的全局性、战略性问题,对国家繁荣发展、人民生活改善、社会长治久安至关重要,为保障国家能源安全,开发南海深水油气资源势在必行。
“深海一号”气田是我国首个自主开发深水气田,区域环境和地质条件复杂,存在“一深一低三高”特点:水深达1547米、海底温度最低2摄氏度、部分区域含浅层气、高投入、高风险、高科技,给深水开发钻完井作业带来极大挑战,具体表现为:
(1)探井转开发井和智能完井工艺复杂,界面管理和控制困难;(2)深水开发井作业周期长、成本高,亟需提升作业效率;(3)深水井筒完整性影响因素多,安全风险高,控制难度大;(4)深水关键装备产品长期被国外垄断,亟需联合攻关实现国产化。
以上挑战给深海气田安全高效开发钻完井带来极大困难,为实现“深海一号”气田安全高效开发,自2013年起,依托国家级、公司级重大项目提供的支持保障,深化企地合作,组建了“产—学—研—用”一体化研发团队和管理团队,形成了包括4项创新成果的深水气田开发安全高效钻完井管理体系,广泛应用于“深海一号”气田开发钻完井工程中,为气田开发提供了强有力的管理支撑和技术保障。
二、“深海一号”超深水气田开发安全高效钻完井内涵和主要做法
海南分公司以“安全、高效”为导向,针对南海深水海域“一深一低三高”特点导致的探井转开发井难度大、开发井长效生产保障困难、安全控制要求高、开发井作业周期长成本高、关键工具装备技术含量高研制困难等问题,建立了深水探井转开发井和智能完井综合管理方法、深水复杂条件优质高效建井模式、深水开发井筒完整性及安全管控方法、深水开发钻完井关键装备与产品国产化研发管理方法,组建了一套高效联合攻关研发管理团队,形成了一套深水气田开发安全高效钻完井管理体系,支撑了超深水气田安全高效开发。
“深海一号”超深水气田开发安全高效钻完井管理体系,主要内容有:
(一)深水探井转开发井和智能完井综合管理方法
建立了深水探井转开发井和智能完井综合管理方法,实现了2口探井转开发井。主要包括:(1)建立了全寿命周期深水探井转开发井综合设计方法。基于精确的管柱完整性分析模拟,形成了以四个“定量因素”和三个“定性因素”控制的深水探井利用可行性综合评估方法。(2)实现2口探井转开发井,在保证本质安全的情况下,节省3.75亿元。(3)形成了双层井下流量调控智能完井设计方法。基于气藏调控需求,兼顾储层保护和井控安全,国内首次设计了深水智能完井创新技术方案,实现了复杂边底水气藏多层系开发井下流量远程监控与避水控制均衡开采等生产制度优化调整。成功实施2口智能完井,直接节省修井成本折现投资约1.2亿元。
1. 全寿命周期深水探井转开发井综合设计方法。深水钻井成本高、周期长,探井转开发井已成为深水油气田开发的主流做法。探井设计虽然考虑后期转开发井功能,但由于地质油藏的不确定性,探井设计阶段并无法完全考虑生产期的产量、组分、井完整性等全寿命因素,在开发阶段仍需对探井转开发井的可行性进行系统全面评估,以确保全寿命井筒安全。以井筒完整性为目标,建立了以三个“定性因素”(满足油藏要求、井口情况、固井质量)和4个“定量因素”(套管材质、强度要求、井筒尺寸、成本)为控制目标的深水探井转开发井作业可行性评估技术,从6口保留井口的探井中优选确定了两口探井转开发井的设计方案。针对6口保留井口的探井,遵循“是否满足油藏要求、井筒是否满足全寿命要求、是否存在重大风险、是否具有经济性”等要素,构建了深水探井转开发井评估方法。
综合考虑开发井靶点布置、油藏要求、井筒完整性以及投资情况,为保证大气田的生产安全和长效寿命,实现2口探井转开发井。
2. 井下流量调控智能完井设计方法。为了满足边底水气田生产管理及后期生产调整的需求,公司首次创新设计了深水智能完井技术方案。该方案实现了双层井下流量监测和调整,同时满足底水气藏的智能控制。在调研国外成功应用的深水智能完井技术及管柱的基础上,从工艺、可靠性角度综合对比了不同控制方式的智能完井技术。最终从可靠性,以及应用情况考虑,推荐陵水气田开发井采用液压智能控制方式。深水气井智能完井技术方案在满足需求情况下的技术可行性基础上,管柱结构设计兼顾了深水作业流程造成的储层保护和井控安全,考虑了后期施工作业的风险、生产后期起管柱时效,减少FIV的开启风险等,最终形成了一套满足深水完井工艺整个生命周期可靠性的智能完井方案。2口智能完井技术,实现了底水气藏的生产全过程精细管理,以及出水后的远程解决方案,避免了由于出水而必须进行修井或关停作业。
(二)深水复杂条件优质高效建井模式
深水开发井作业周期长、成本高,非生产时间居高不下,对深水油气开发影响较大。针对深水开发井钻完井作业特点开展研究,揭示了深海钻采管柱在南海特殊环境和船舶运动耦合作用下的动态响应规律,创建了深水开发分层次规模化批钻批完作业模式及水下采油树高效安装方案,首创了深水开发上下部一体化完井作业模式,大幅提高作业效率,形成了一套“深水复杂条件优质高效建井模式”,主要包括:
1. 深水开发井分层次规模化作业模式。构建隔水管力学状态分析模型,形成了悬挂隔水管多井次大范围井间移位技术,基于气田水深跨度、井位布置特点,综合评估平台能力、作业风险,创新突破了分井段、分时段规模化作业方式。创建了规模化技术,基于气田空间展布、水深跨度、井位布置特点,综合评估作业平台能力、各井段钻完井风险,创新突破了分井段、分时段规模化作业方式,奋进号、海洋石油982与蓝鲸号平台协同作业,建立了基于批钻适应性决策模型的表层规模化批钻作业模式,建立了悬挂隔水管工况分析模型和约束边界,研究了南海区域风、浪、流特点,确定了平台悬挂隔水管工况边界条件,揭示了航行过程中隔水管力学状态变化规律。建立了不同表面流速悬挂航速图版,运用神经网络的方法对航速进行预测,制定了台风极端工况应急响应决策方法,建立了考虑作业安全窗口的批钻最优方案及航行最优方案选择模型,优选了批钻最优化方案,实现表层规模批钻。相对于国外每口井均需起下BOP,累计完成15次悬挂防喷器组航行,节省起下防喷器组时间约52.5天,节省费用约1.5亿元,创水下防喷器组连续作业时长110天纪录;悬挂BOP航速由0.3节提升至0.5节,效率提升66%。
2. 水下井口及采油树高效安装方案。该方案建立基于洋流参数影响的采油树树体及下放管柱—BOP本体及下放管柱双线管柱模型,进行了来流方向、波浪方向、流速和浪高对双线管柱总体偏移的影响和受力分析,揭示了深海钻完井管柱在南海特殊环境和平台运动耦合作用下的动态响应规律,完成了不同流速和浪高对管柱顶端、中端和底端最大应力的影响测算,系统评估了双线管柱下入过程管间扰动和碰撞风险,形成了采油树树体及下放管柱—BOP本体及下放管柱双线管柱下入作业安全窗口,建立了水下井口及采气树快速稳定安装方案,首次采用悬挂BOP同时下入采气树的作业模式,充分利用双井架,在不起出隔水管及BOP的条件下,根据海流流向剖面选择平台最佳艏向,通过双ROV多角度实时扫描分析水下采气树与BOP方位和距离,实现了在不起水下防喷器的情况下完成水下采气树的下入。单次可节约起、下防喷器及其保养试压工期9天,与工程船下树设计工期相比,提效2倍以上。
3. 深水开发上下部一体化完井作业模式。国际上通用深水分开式完井程序为“下部完井、下桥塞临时弃井、转至下口井、井筒重入、上部完井、清喷作业”,完井作业步骤复杂,设备多、转换快。该模式建立了深水平台紧凑空间完井装备快速安装方法,形成了地面放喷设备模块化+防砂地面设备模块化的模块化作业模式,减少装备占用甲板面积40%以上,吊装时间减少25%,可快速安装完井装备;形成了一体化远程智能监测及控制技术和作业机具适应性升级方案,完成了45项作业平台适应性改造升级,在此基础上,依托管理模式升级,建立了“下部完井、上部完井、清喷作业”上下部一体化完井,突破国际上深水上下部分体完井模式,无需临时弃井和重入,实现完井后立即清喷,单井减少储层浸泡时间180天以上,累计节约工期50船/天。
(三)深水开发井筒完整性及安全管控方法
针对深水开发井筒完整性及安全管控影响因素多,实施难度大的特点,工程技术作业中心作为管理核心,突破传统技术与管理模式,协同组织相关单位及科研院所进行科技攻关,基于本质安全理论,考虑台风天气、深水井筒封固和流动安全特殊性,构建了深水井筒完整性管理模式和流动安全保障预测与防治管理,形成了深水开发井钻完井应急处置方法,保障了“深海一号”气田安全高效零事故实施。
1. 多因素耦合影响多级屏障井筒完整性管理模式。该管理模式主要是通过分析南海深水开发井井筒风险产生的原因及其可能产生的后果以及构建各风险之间的相互制约关系,将深水开发井井筒风险划分为井况与环境风险因素、井筒失效风险因素、钻完井设备风险因素和操作与管理风险因素4个评价单元,并确定了深水钻完井作业风险评估的42个评价指标,考虑各个风险评价指标的严重程度与发生可能性以及各个评价指标之间的相对重要性,利用风险矩阵法得出各个评价指标的严重程度和发生可能性,并计算其相应的风险值,再采用层次分析法计算各个评价指标的归一化综合权重,最后计算整个深水开发经钻完井作业的风险度,从而结合风险矩阵法和层次分析法建立风险评估模型。
建立冲蚀—腐蚀耦合模拟实验装置,采用高速旋转的叶片带动砂粒模拟冲蚀,实现了冲蚀和腐蚀的耦合作用。通过管材冲蚀—腐蚀试验,建立了冲蚀—腐蚀速率预测模型,创新了冲蚀—腐蚀耦合影响的管柱变形破坏分析方法,形成了考虑冲蚀—腐蚀耦合效应的深水开发井井筒强度优化设计方法。创建了深水开发井“生产套管封固+密封总成+井口锁紧短节+地层隔离阀+井下安全阀+水下采油树堵塞器”的6级屏障井筒完整性保障技术,构建了“技术套管水泥浆返高界限+C环空破裂盘+B环空弹性隔离液+A环空压力监测控制”的4层次环空压力管理方法。
2. 深水井筒流动安全保障分析方法与防治管理模式。建立了基于井筒“变梯度、多边界、有节流、含相变”复合热量传递机制的温度场动态预测模型,首创了井筒水合物沉积厚度定量精细表征方法和高效防治技术,综合考虑复杂深水海洋环境、非牛顿流体测试液对井筒温度场的影响,首次揭示了海水—隔水管—环空流体多边界多梯度复合热量传递交互作用机制,建立了管柱入井—开井放喷—关井求压全周期温度场动态预测模型,预测精度由传统方法的不足50%提高到95%以上。建立了基于水合物生成热力学、沉积动力学和水合物颗粒管内受力状态分析的深水气井测试水合物颗粒生长沉积模型,提出了基于安全作业窗口的“防治堵塞,允许少量生成”全寿命周期水合物防治新方法。针对“深海一号”气田30年寿命周期,开展了全生命周期流动保障安全专题设计,利用深水探井测试及YC13—4、LW3—1气田开发井数据进行校核,温度、压力数据偏差在7%以内,验证了温压场模拟数据的可靠性,在测试井瞬态及开发井稳态模拟工作中,通过多次的拟合,总结出一系列能更加准确的反映南海区块深水气田生产状况的建模方法,形成了一套完整的全寿命周期井筒流动保障方法,涵盖稳态生产、瞬态启动、计划关井、非计划关井、冷启动、热启动等各个工况的分析,指导了井下化学药剂注入点的设置、井下安全阀深度设计、油管尺寸的定制、水下采气树材料要求及低温冲击测试、清井排液水合物防治、开关井制度的制定等防控需求,实现井筒零堵塞。该管理模式已成功应用于“深海一号”气田开发,为我国首个自营深水气田长效安全生产提供了强有力的管理支撑。
3. 深水开发井钻完井应急处置方法。构建了高风险关键作业应急解脱技术与处置方法,首次成功应用大尺寸电液控制水下测试树,可实现高风险关键作业在极端天气下的应急解脱与回接。科学决策、高效应对台风,建立了一套“早预警、早决策、早返回”的深水完井防台处置方法。建立了钻井装备与工程施工机具联合作业时间窗口优化管理,精确计算时间节点,严格按照避让距离要求,避免发生碰撞。首次成功应用大尺寸电液控制水下测试树:7—3/8″10K NGLS大尺寸电液控制水下测试树是坐落管柱的重要组成部分,在紧急情况下可以提供2道安全屏障,并且能在15秒内完成从管柱中解脱,确保平台的安全。“深海一号”气田开发钻完井作业经历了8个台风、最大风力15级的考验,作业全过程零安全事故。
(四)深水开发钻完井关键装备与产品国产化研发管理
该管理模式主要是由工程技术作业中心基于作业需求,凝练关键设备技术指标与性能要求,同时作为管理核心,组织厂家进行设备工程攻关研制,并推动装备现场示范应用与迭代优化。
先后研制了深水开发井固井、防砂、系统试井关键工具及关键配套系统,形成了系列国产化产品,打破了国外垄断,大幅降低了作业成本,实现了深水气田开发自主安全高效实施,并为今后关键装备国产化形成了一套高效联合攻关研发管理模式。
1. 深水开发井固井关键工具产品国产化。牵头研发了远程控制轻型深水固井水泥头,该水泥头的待机时间超过72小时,达到了国外同类主流产品的水平,整机重量不超过2.4吨。采用分体式旋转注入结构,便于V组密封更换;推力圆锥滚子轴承,可承受偏心载荷;环空流道设计,加工制造简单;三级胶塞释放指示;主体之间采用大螺距梯形螺纹连接,圆柱锁销定位并承扭;采用远程无线控制系统,满足1区防爆要求;系统自带气源和电池组,气源可满足10余次操作;采用多频共享、无线跳频及数字加密技术,抗干扰能力强;具有逻辑互锁保护功能;集成式阀块,无外接管线,安装维护便捷;可有效保障现场作业需要。自主研发了以低水化热增强剂为核心的低温早强水泥浆体系,具有高悬浮性、高水泥浆强度、低放热和低温促凝的优点,解决了低温下(2摄氏度)水泥浆早期强度不足的难题。
2. 深水高产气井长效防砂系列关键工具装备国产化管理模式
在该管理模式的指导下,公司研发了多流道旁通筛管,并创新采用了“月牙形”结构设计、旁通管圆周同心布置和旁通管上充填口对称设计,与国外同类产品相比,我们外径降低了6%,旁通管过流面积增加了8%,从而降低了压力损失。此外,我们还研发了快速连接组件,现场不需要再对接旁通管,提高了作业效率。与国外同类产品对比,在最大外径、旁通输送面积、结构设计、连接方式等方面具有优势。相比于国外同类产品,节约成本60%以上,应用于“深海一号”气田开发钻完井项目中6口井次,累计应用1970米。研发了深水砾石充填井下可视化压力计,首次实现了深水水平井砾石充填全过程压力动态监测,揭示了砂浆运移全路径温压变化规律。多流道旁通筛管和充填井下可视化压力机应用于“深海一号”气田完井防砂,所有井均高质量完成砾石充填作业,充填效率全部达130%以上。
针对常规防砂地面设备就位耗时长,通用性差,占地广的问题,创新建立防砂地面设备模块化系统作业模式,建立撬架有限元力学分析模型,基于模块载荷工况、模块化稳定性及安全性模拟分析,优化设备和流程布局,建立了超深水完井地面防砂设备模块化技术,实现吊装次数降低25%,安装时间缩短50%,设备占地面积降低30%,该管理模式有望在今后现场防砂作业中进行大规模应用。
3. 深水开发井系统试井关键装备系统国产化管理。该管理模式主要是指导研发了深水开发井系统试井高速流动条件下的井底—井筒—地面全流场数据采集监测系统,建立了深水试井高速流动条件下的井底—井筒—地面全流场数据监测、采集、仿真分析方法,通过高度集成采集服务器、数据工作站、数据客户端等核心子系统,实现单台工作站即可满足现场储层物性、流体物性、安全风险、测试管柱、地面流程、作业方案、数据采集传输等8大类150余项关键参数的采集需求,参数准确性达95%。实现了高速流体地面多级分布式安全管理技术,建立了井口多级节流与控制系统,缓解了节流效应导致的井口极低温,研发了环保型智能低噪音燃烧装置与高温高噪分布式监测及控制管理系统,建立了超高速流体地面多级分布式安全管理技术,实现地面测试流程全过程动态仿真。研发了井口含砂量、管线壁厚及井口震动三位一体的监控系统,研制了内外激光多气组分原位扫描装置,实现了油—气—水—砂三相四组分实时精确识别和流动风险管理;建立了不同安全序列分级控制及远程响应系统,应急关断响应时间由15秒缩短至4秒以内。
三、“深海一号”超深水气田开发安全高效钻完井管理创新与实践的实施效果
(一)应用效果
“‘深海一号’超深水气田开发安全高效钻完井管理创新与实践”项目成果全面应用于“深海一号”大气田11口井钻完井作业、陵水25—1深水高温高压气田12口井设计方案,深水钻完井安全性和作业效率得到全面提升,部分关键产品及工具实现国产化,打破了国外垄断,并带动了国内相关企业进行技术创新和产业升级,同时降低了作业成本,实现了深水开发井自主安全高效作业,钻完井成本控制良好。后续将推广应用于陵水25—1深水高温高压气田开发钻完井作业、陵水18—1/18—2超深水气田勘探开发以及南海中南部油气资源勘探开发,为南海万亿大气区建设提供重要保障,具有良好的推广应用价值。
“深海一号”开发项目是我国首个自营深水气田的开发,将会带动粤港澳大湾区及海南岛的发展,成为南海重要的清洁能源生产基地,为粤港澳大湾区及海南岛的经济发展提供清洁能源,有力拉动地方经济的可持续发展。深水气田开发安全高效钻完井管理体系的创新使中国系统掌握了深水钻完井核心管理方法,抢占了世界油气勘探开发的制高点,使中国成为南海周边唯一具备独立开发深水油气资源能力的国家,取得了显著的社会效益。
(二)经济效益
该成果为南海深水油气田钻井作业安全高效实施提供了有力的保障,应用于“深海一号”气田11口深水开发井,使深水钻完井作业安全性和效率得到全面提升,总体成本控制效果良好,钻井累计节约工期101.4天,节省钻井成本4.43亿元,完井累计节约工期181.3天,节约完井成本13.02亿元,钻完井累计节省17.45亿元,按管理成果贡献率系数0.75,再扣除科研支出费用779万元,贡献经济效益13.01亿元。
“深海一号”气田通过全寿命周期深水探井转开发井设计与实施,实现2口探井转开发井,节省投资5亿元,按管理成果贡献率0.75,贡献经济效益3.75亿元。
作者单位:中海石油(中国)有限公司海南分公司
成果其他创造人:黄 熠 蒋东雷 马传华 苏剑波 柳亚亚 徐 斐 董 钊 吴艳辉 刘智勤
点评一
开启探索深海油气资源新纪元
□ 文\中新国际能源研究院 朱昌海
走向深海是当今世界油气工业由常规资源走向非常规资源,从陆地走向海洋一个不可逆转的大趋势。根据美国地质调查局(USGS)评估数据,全球海洋油气技术可采储量分别为1.097万亿桶和311万亿立方米,分别占全球油气技术可采总量的33%和57%,其中大部分位于水深1500米的深海海域。
全球海域油气勘探开发步伐明显加快,储产量实现稳步增加,特别是深水、超深水,一直是5大国际石油公司(壳牌、埃克森美孚、bp、道达尔能源、雪佛龙)深耕的热点领域,超深水油气产量增速超过深水,已成为全球油气资源的战略接替区。2022年全球深水、超深水领域共获得21个大中型油气田发现,可采储量20.06亿吨油当量,储量同比增幅达86.42%;2022年,全球深水油气产量进一步提至1010万桶油当量/日,占全球油气产量的6.4%。
随着巴西、圭亚那等地区深水油气产能的进一步释放,全球深水油气产量在2030年有望突破1700万桶油当量/日,届时全球10%以上油气供应来自深水,较2022年大幅增长近71%。在这一背景下,美欧日印等国家和地区先后将海洋油气特别是深海油气资源作为国家战略资源纳入国家政策视野,并将开发海洋油气资源提高到国家战略高度。
尽管参与深水油气开发的国家逐渐增多,但全球深水油气产量仍集中在以美国墨西哥湾、巴西、西非为主的国家和地区。巴西、美国、安哥拉和尼日利亚这4个国家合计深水油气产量为3.28亿吨油当量,占全球深水油气产量的65%。深水油气开发的高投资、高技术、高风险等特征,对参与的石油公司设置了非常高的进入门槛。
上天、下海、入地,是人类探索自然的三大壮举。上天难,下海更难。海面下水深每增加一米,压力、温度、涌流等情况就会完全不同,开发难度呈几何倍数增加。数百米的海水不是一条线,而是摆在海洋石油人面前的一道鸿沟。由浅入深,海洋石油人化茧成蝶,实现了从浅水思维到深水思维的艰难转变,将无数的不可能变成了可能,败绩变成了奇迹。
中海石油(中国)有限公司海南分公司针对南海深水海域“一深一低三高”特点导致的探井转开发井难度大、开发井长效生产保障困难、安全控制要求高、开发井作业周期长成本高、关键工具装备技术含量高研制困难等问题,建立了深水探井转开发井和智能完井综合管理方法、深水复杂条件优质高效建井模式、深水开发井筒完整性及安全管控方法、深水开发钻完井关键装备与产品国产化研发管理方法,组建了一套高效联合攻关研发管理团队,形成了一套深水气田开发安全高效钻完井管理体系,支撑了超深水气田安全高效开发。该成果为南海深水油气田钻井作业安全高效实施提供了有力的保障,应用于“深海一号”气田11口深水开发井,使深水钻完井作业安全性和效率得到全面提升,总体成本控制效果良好,钻井累计节约工期101.4天,节省钻井成本4.43亿元,完井累计节约工期181.3天,节约完井成本13.02亿元,钻完井累计节省17.45亿元,按管理成果贡献率系数0.75,再扣除科研支出费用779万元,贡献经济效益13.01亿元。
海洋之于海洋石油人,正如土壤之于树木。步入深水,就是这棵大树不断向深处、远处扎根,汲取更多养分的过程。前不久,“深海一号”能源站再次“上新”技能——完成台风远程遥控生产改造,能够实现恶劣天气不掉线、台风期间不停产,每年可新增6000万立方米天然气产量。
70千米外,“深海一号”二期工程正进行深水海管铺设作业,建成后可使“深海一号”天然气储量从1000亿立方米增至1500亿立方米,高峰年产量从30亿立方米增至45亿立方米。
“深海一号”傲然面世,向世界展示了中国技术、中国设计、中国装备、中国速度、中国力量、中国精神。
中国号“钢铁巨轮”必将风雨无阻,向着广袤的海洋展开翅膀,为探求深海油气资源开启新纪元。
点评二
“大国重器”为国家能源安全再添筹码
□ 文\本刊特约评论员 时光
在海南陵水海域,蔚蓝的海面上矗立着一个明黄色的钢铁“巨人”,这是全球首座十万吨级深水半潜式生产储油平台“深海一号”,第一个由中国人自主研发、设计、建造的自营深水大气田。
平台上活跃着身着火红工装的深海“铁军”——中国海油海南分公司“深海一号”开发生产团队。这支年轻人为主体的团队,成功开发运用3项世界首创、13项国内首创技术,攻克几十项行业技术难题,使我国海洋石油工业一举实现从300米向1500米水深挺进的重大跨越,推动中国海洋油气勘探开发全面进入“超深水时代”。
2021年1月14日,中国海油对外宣布由我国自主研发建造的全球首座十万吨级深水半潜式生产储油平台——“深海一号”能源站在山东烟台交付启航,于同年6月25日在海南陵水海域正式投产,用于开发我国首个1500米深水自营大气田——陵水17—2气田。至此,凝结着几代中国海油人接力攻关的大国重器“深海一号”,把传说变为现实,无数中国海油人不畏艰难、奋勇争先、开创先例,叩开了超深海能源宝藏的大门,每天1000万立方米的天然气自海底1500米源源不断地开采出来,最终抵达千家万户,化为袅袅炊烟。
挺进深海,创造的不只是地理深度,更是一个充满希望的未来。
海平面以下,水深每增加10米,水下设备就要多承受1个大气压的水压;当水深超过1000米时,海水温度会从平均十几摄氏度降至约5摄氏度,从而对油气的状态产生影响;到达海底,巨大而松软的沙坡沙脊会让生产设备难以稳固着陆,更不用提南海常见的内波流和台风天气。位于琼东南盆地的“深海一号”大气田被发现,其探明天然气储量超千亿立方米,最大水深超过1500米,最大井深超过4000米,是我国迄今为止自主发现的平均水深最深、勘探开发难度最大的海上超深水气田。深水油气田开发是世界级难题,对于海洋石油开发起步较晚的中国而言,更是难上加难。
面对困境,“深海一号”开发生产团队带领数千名施工人员,克服重重困难,昼夜轮流作业,高质量完成了船体建造、上部组块建造,以及两个组块的“大合龙”。2020年底,中国海油仅用1年半时间建成该平台,创下了比国际同类平台建设工期提前18个月的纪录。
我国是油气进口第一大国,2020年我国油气对外依存度分别升至73.5%和43.2%。也就是说,在我国消费的油气资源中,每100吨就有73.5吨、每100立方米就有43.2立方米来自国外市场。在地缘政治“裂痕”加深、产油国动荡加剧、逆全球化暗流涌动的当下,我国能源安全面临巨大挑战。“深海一号”的成功研发和投产,对于我国能源安全和经济发展具有重要意义。虽说绕开马六甲海峡,解困霍尔木兹海峡能够解决我们“输血”问题,但终归只是治标不治本,而要从根本上解决通道安全问题,还需在构建自己健康完整的“造血”系统入手,而伫立于油气资源富集的南海之上的“国之重器”——“深海一号”,则为我国能源安全再添重量级筹码。
从“深海一号”能源站到“深海一号”大气田,一次次突破的背后,饱含着海油人孜孜不倦的探索与追求。近10年,从荔湾3—1深水气田、流花16—2深水油田群到陆丰15—1油田群等一系列重大油气发现相继进入工程实施和开发生产阶段,海洋石油人肩负着守卫国家能源安全使命,将钻头一寸寸伸向更深邃的海洋。
如今,中国海油几十座各类大型装备,为世界30多个国家和地区提供油气勘探、钻井、安装、生产等多项服务,足迹遍及北欧、中东、东南亚、远东、非洲、美洲等6大区域,成为“一带一路”上的一张蓝色名片。一个个深耕蔚蓝的大国重器正在向世界展示一个创新、开放、活力、激扬的中国海油,以及在战天斗海中展现出来的“爱国、担当、奋斗、创新”的新时代海油精神!

983
点击量
2
下载量
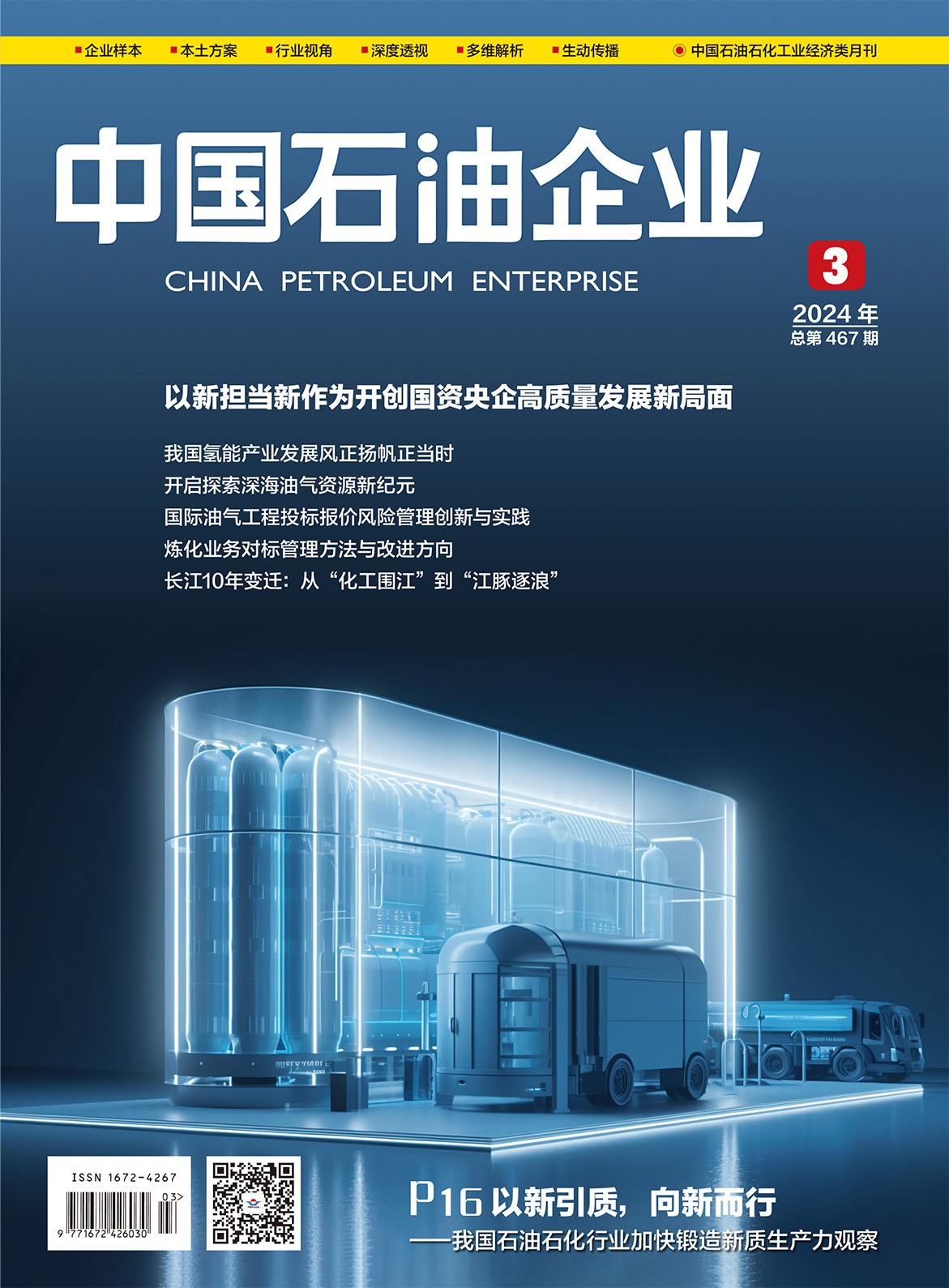
刊出日期:2024.03
主管单位:中国石油天然气集团有限公司
主办单位:中国石油企业协会 中国石油企业协会海洋石油分会
国际标准刊号:ISSN 1672-4267
国内统一刊号:CN11-5023/F
国外发行代号:M1803
国内邮政编码:100724
广告经营许可证号:京西工商广字第0433号(1-1)