5S现场管理起源于上世纪50年代的日本,是指对生产现场中各生产要素所处的状态不断进行整理、整顿、清扫、清洁,以及提升人的素养活动。由于整理(SEIRI)、整顿(SEITON)、清扫(SEISO)、清洁(SEIKETSU)、素养(SHITSUKE)这五个词在日语的罗马拼读中第一个字母均是“S”,所以简称“5S”,又被称为“五常法则”。第二次世界大战前,日本产品质劣价廉,曾是劣质品代名词。但由于价格低,尚可对外出口。二战后,由于美国非但未受战争损害反而大发战争财,而欧洲也在1947年马歇尔计划援助下快速复兴,日本在美军管治下生产受限,劣质产品又难以出口,于是开始在美国质量专家帮助之下走上改进产品质量之路。而糟糕的环境下很难产出高质量的产品,于是5S应运而生。
为了撕掉“质劣价廉”标签,日本制造业从改善现场秩序入手,实施了质量领先战略。经过10年实践,日本制造业发生了脱胎换骨的变化,质量迅速提升,奠定了其经济大国地位。5S现场管理模式,也由此成为世界级优秀企业基本管理配置,是提升管理的基石。
我国改革开放之初,便开始向日本企业学习全面质量管理,把5S管理模式引进国内,并在企业中推广应用。根据国资委数据,上个世纪90年代,5S覆盖了88%国企和62%民企,覆盖面之大前所未有。但今天再谈起这个词,大多企业都会扼腕叹息,流露同一个尴尬表情。
在国外行之有效的5S现场管理模式,在国内缘何失灵,陷入尴尬境地?
5S失灵深层分析
数量庞大的企业在实施5S活动之后,效果并不理想,大多企业5S很难维持,整理、整顿、清扫成果不易保持,极易反弹,重回“浑、混、浊”与“脏、乱、差”局面。正如学界分析那样,在我国推行5S活动的企业90%都没有成功。目前,对于5S失灵分析主要有以下几种情况:
一是过分夸大或期望过高5S功效。企业为了提高产品质量在选择管理方法时,更多的是听取咨询公司或某些专家意见。一些咨询公司和专家在推荐5S时,往往忽略每一种方法应用都需要前提条件,在不了解这种前提条件是什么的情况下,采取拿来主义夸大其功效,期望企业接受。企业经营者往往不是专家,也不可能了解和掌握5S都需要哪些前提条件和应用要件。在信息不对称条件下,企业只能过高地期望5S实施之后的功效,且在无法把握最终效果的情况下就开始仓促上阵,推而广之。5S实施之初,的确也会收到一定成效,起码厂区环境焕然一新。但是,由于缺乏了解5S适用性了解,其效果也随时间开始递减,最后则流于形式,成为一种摆设。5S是一个体系而不是单独的一次活动,因而短期行为不会给企业带来任何好处。不少企业期望通过一场运动来迅速改变现场脏乱差及人员素养低下的状况,好似来点灵丹妙药,常不惜重金请来顾问团队进行变革。这样想法可能有些天真,容易出现“一紧二松三垮台四重来”的局面。
二是忽略5S内在要求。5S活动最关键的环节是素养,而且这五种形态前四种都是可以量化的外在反映,只有素养是无法量化的内在要素,同时也是前四项能否顺利实施的前提条件。个别企业往往把5S失效责任都推卸到员工身上,“员工素养低”成为企业经营者开脱责任的一种理由。有些企业领导自身素质不高,将企业规章制度都视作是针对员工的。他们可能喜欢“成功学”课程,被“大师”忽悠得七荤八素,做事急功近利,奖惩随意、朝令夕改,随心所欲。事实上,凡能以身作则、严于律己的领导,其所在企业的现场5S都不会差。须知企业领导在现场的点滴行为,都会对员工产生巨大影响。三是应用过程缺少系统性。5S应用于日本企业之中,与美国人爱德华·戴明有直接关系。戴明是位有故事的管理大师。1939年戴明加入美国联邦统计局时,深入研究现场管理与应用问题,并建立起自己的管理体系。对戴明管理方法的引入,大幅改善了日本产品质量。日本企业把5S融入产品质量管理之中,广泛地运用,使戴明全面质量管理体系更加完善。可见,如果没有戴明的基础,仅仅依靠5S,是不可能使日本制造发生根本性变化的。我国企业开展5S之所以“虎头蛇尾”,与企业经营者缺乏对全面质量管理系统性理解有着直接关系,认为只要轰轰烈烈地开展起开,就可以建立起长期而有效的质量管理体系,这几乎是不可能的。四是对5S管理缺乏层次和维度思考。5S第一个层面是现场管理,这需要管理者对生产现场摆放的各种物品进行甄别和分类,区分什么是需要的,什么是不需要的。第二个层面除去有形的层面,还有无形的层面需要整理:员工在流水线上移动;物料输送和搬运流程;信息沟通渠道等。第三个层面是延伸层面,不仅要站在有形、无形之上,还要站在整个生产企业运营层面上,也就是制造业企业需要对客户与供应商加以“整理”。即利用1S整理出ABC类客户,信誉度不好的客户其制约条件与优质客户是不一样的。同样,对于供应商也是如此,即利用5S中整理概念与思路整理出需要的客户与供应商,并与之建立良好的合作。
对于5S失效的解释,管理者可以从不同角度做出不同判断。但是,这些并非深层原因,而是表现。把表象误作原因,当然解决不了深层次问题。
所谓“橘生淮南则为橘,生于淮北则为枳,叶徒相似,其实味不同。所以然者何?水土异也。”这就是说,同一个物种会因为环境改变而出现变异。新制度经济学认为,制度具有互补性,即制度顺利运行依存于其所处的历史、法律、社会、技术、政治和经济环境,因而一种制度的移植必须有与之互补的环境相配合。5S作为一种源自日本的制度安排,在往我国企业移植时当然也需要有与之互补的环境,其推行失灵的主要原因,也将体现在与日本环境的差异性上。
日本企业大多实行终身雇佣制,员工归属感强烈。这种“家文化”对5S实施起到了积极推动作用。而我们并不具备日本在发展5S过程中,所具备特定的有利于其推行的互补性条件,这才是我们推行5S失灵的深层原因。因而,构建“家文化”经营体系,是推广5S管理及应用其他管理方法的关键所在。从某种意义上说,5S管理是建立在以人为本基础上的,了解员工的工作环境,满足员工的工作需求,才能使5S管理更具实效。
寻找5S有效融合之道
首先,正确认识是有效开展5S的前提。无数事实表明,仅仅依靠5S对于产品质量提高只能起一时之功效。要想长期保持产品质量的稳定性和持续性,必须建立起全面质量管理(TQM)控制体系。就其TQM体系而言,是由多种方法和工具所构成的,5S活动、看板管理、IE方法、PDCA循环,以及其他各种统计分析定量与定性方法等。因此,作为企业经营者一定不能把5S作为提高产品质量的唯一方法。除对TQM系统性了解或掌握外,还需要正确把握企业成长不同阶段需要解决的主要问题,以及为了解决这些问题需要采用的不同方法。一般来说,这些方法既可以独立使用,也可以组合使用,无论使用何种方法,主要是由于企业发展阶段、目标定位、发展水平,以及员工接受能力等因素决定。例如,企业在发展初期,许多成长要素都处于不稳定之中,此时推行5S成功率非常低。如果企业在行业龙头地位,就需要全方位应用TQM各种方法。
其次,构建“以人为本”的企业文化经营体系。无论是应用何种管理方法,最终这些方法都是由“企业人”来完成的。“企业人”是推广5S及应用其他方法的关键所在,将员工素质差异化的“社会人”,转变成素质同质化的“企业人”,这个过程往往需要长期教育和培养才能实现。
再次,建立以效率为基础的企业运营系统。客观地说,提高产品质量是一项细致性的工作过程,也是一项复杂的系统工程。如果仅仅是为了提高产品质量,相信企业通过“慢工出细活”方式,都有能力来取得预期效果。但这种方式会降低产量进而影响企业效益,因此,平衡产量与质量之间的关系又成为企业需要解决的问题,即如何保证产量前提下不断提高产品质量,同时又如何保证质量的前提下不断提高产量。
“鱼和熊掌”兼得的唯一方法,就是建立以效率为基础的企业运营系统。效率是由时间与工作量这两个要素所决定的,那么提高效率主要从两个要素入手,通过三种方法来实现。一是在工作量一定的条件下,通过时间合理安排来达到减少时间上的浪费,把有限的时间都用在工作上。如通过5S、六西格玛活动等都可以达到这样的预期;二是在时间一定的条件下,通过合理地安排工作量来达到提高工作效率。例如,通过看板管理方式就可以达到这种效果;三是将时间与工作量进行有机组合,来最大程度地实现细微工作的动作经济。提高工作效率除采用各种方法外,最重要的是循序渐进,任何一种提高质量的方法都是需要一定条件才能完成的。例如,六西格玛活动一定是建立在5S基础之上的,任何一种不考虑前提条件的做法都难以取得预期效果。

479
点击量
0
下载量
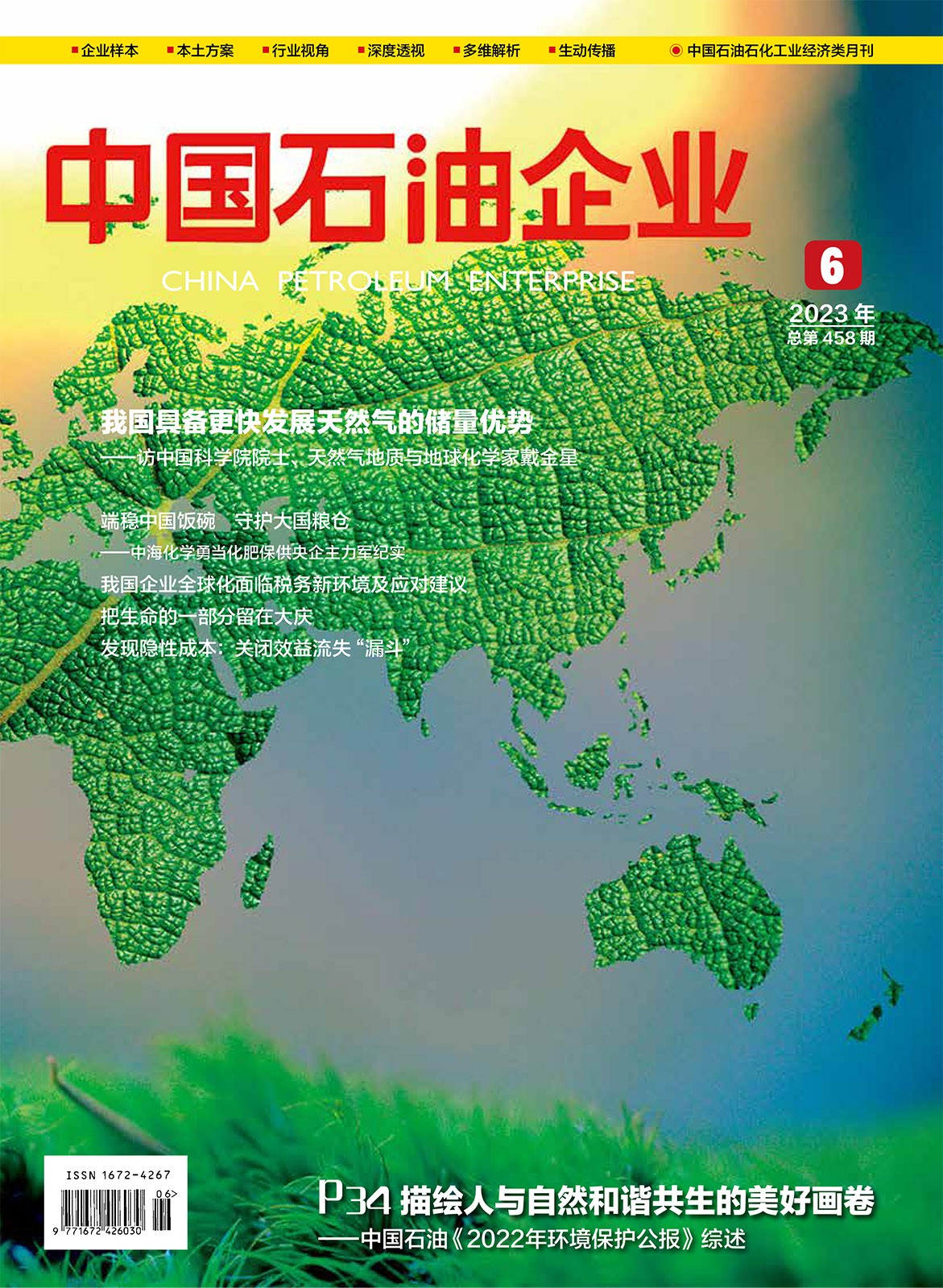
刊出日期:2023.06
主管单位:中国石油天然气集团有限公司
主办单位:中国石油企业协会,中国石油企业协会海洋石油分会
国际标准刊号:ISSN 1672-4267
国内统一刊号:CN11-5023/F
国外发行代号:M1803
国内邮政编码:100724
广告经营许可证号:京西工商广字第0433号(1-1)